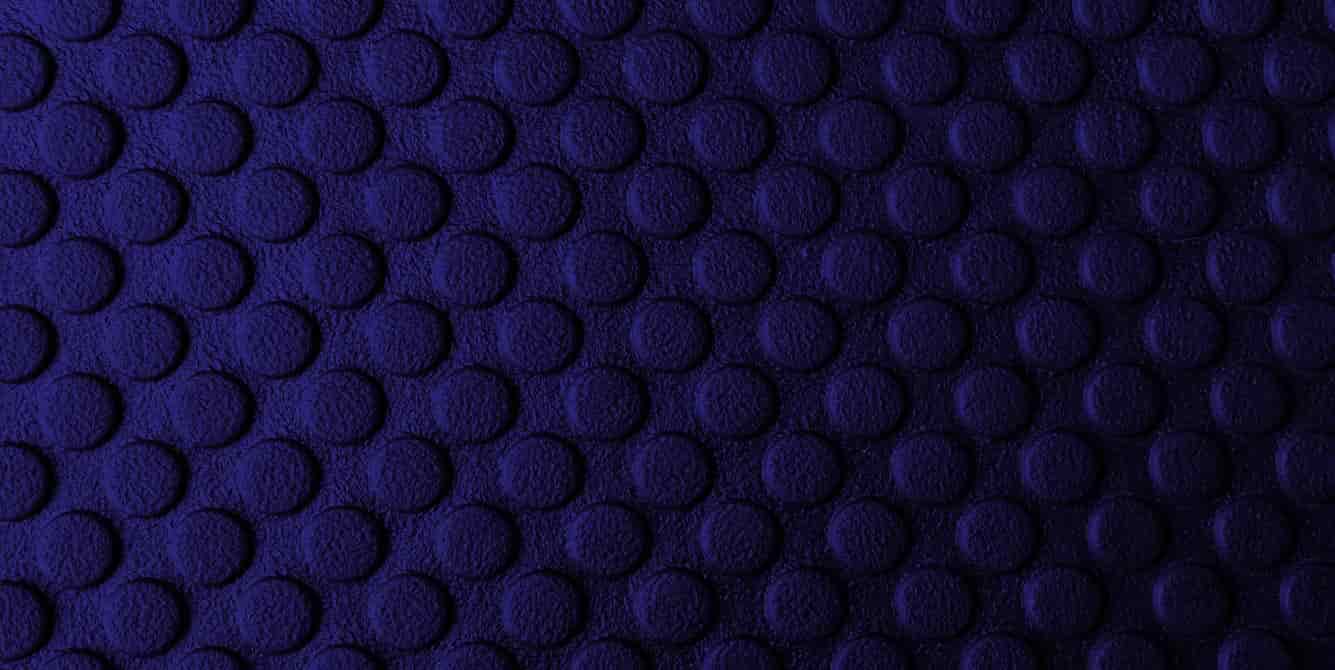
Material Selection
This material selection guide is meant to provide a solid understanding of the processes, questions and technical considerations involved in the design and manufacturing of custom rubber products.
The material selection process involves asking the right questions concerning the application and environment the part will be exposed to. Rubber compounds are all unique in their own way, and asking the right questions during the selection process enables us to match the right compound to the part. By understanding some of these considerations, you are better able to control the cost of your product while achieving the proper performance levels.
Some common questions we might ask are:
What is the application or function of the part?
Knowing how a material will be used in its end-use application is imperative during the material selection process. Will the part:
- Transmit energy?
- Absorb energy?
- Transmit a fluid?
- Provide structural support?
- Seal a fluid?
Is there a cost target for a material that we should consider?
- Material cost per part?
- Material cost per pound?
Will the part be located inside or outside?
- UV exposure that may affect properties or color?
- Time length of exposure?
- Temperature during exposure?
What, if any, are the temperature requirements?
- Maximum service temperature?
- Minimum service temperature?
- Constant use temperature?
- Length of exposure to different temperature extremes?
Is there exposure to specific chemicals?
- Acids
- Bases
- Oils
- Others
- Time length of exposure?
Will the part be exposed to an abrasive environment?
Are there any physical property requirements?
- Tensile strength?
- Tensile elongation — need to stretch without breaking?
- Tensile stress?
- Hardness?
- Compression set (at temperature) — resistance to set under extensive load?
- Flexural modulus — resistance to deformation?
- Tensile set (at temperature)?
- Specific gravity target?
- Viscosity or melt flow requirements?
Does the part need to absorb vibration?
Is the part being used as a sound dampener or deadener?
Does the part need to meet any regulatory requirements?
- Flame retardant to UL or other agency standard?
- Comply with FDA or NSF food or water contact?
- Meet a specific automotive specification?
- Comply with USP class VI for a medical device?
Not all of the properties requirements above may apply to your products applications. By engaging us in the proper dialogue, and based upon the answers to the above questions, we can recommend a material to suit the application and environment of the part.
Elastomer Hardness Selection
Thermoset rubber materials are available in durometers ranging from 20 Shore A to 90 Shore A, while even harder materials are available for thermoplastic elastomers on the Shore D scale. Commonly, materials hardness range in most general applications from 50 Shore A to 80 Shore A, with the majority of sealing products being made from materials with 70 Shore A hardness. Depending on your specific application, Timco Rubber will be able to recommend a proper hardness for your rubber material.
In dealing with very hard or very soft materials, some manufacturing limitations will apply. Parts that have a complex geometrical design or deep undercuts are more difficult to manufacture from very soft (less than 30 Shore A) or very hard (greater than 80 Shore A) materials.