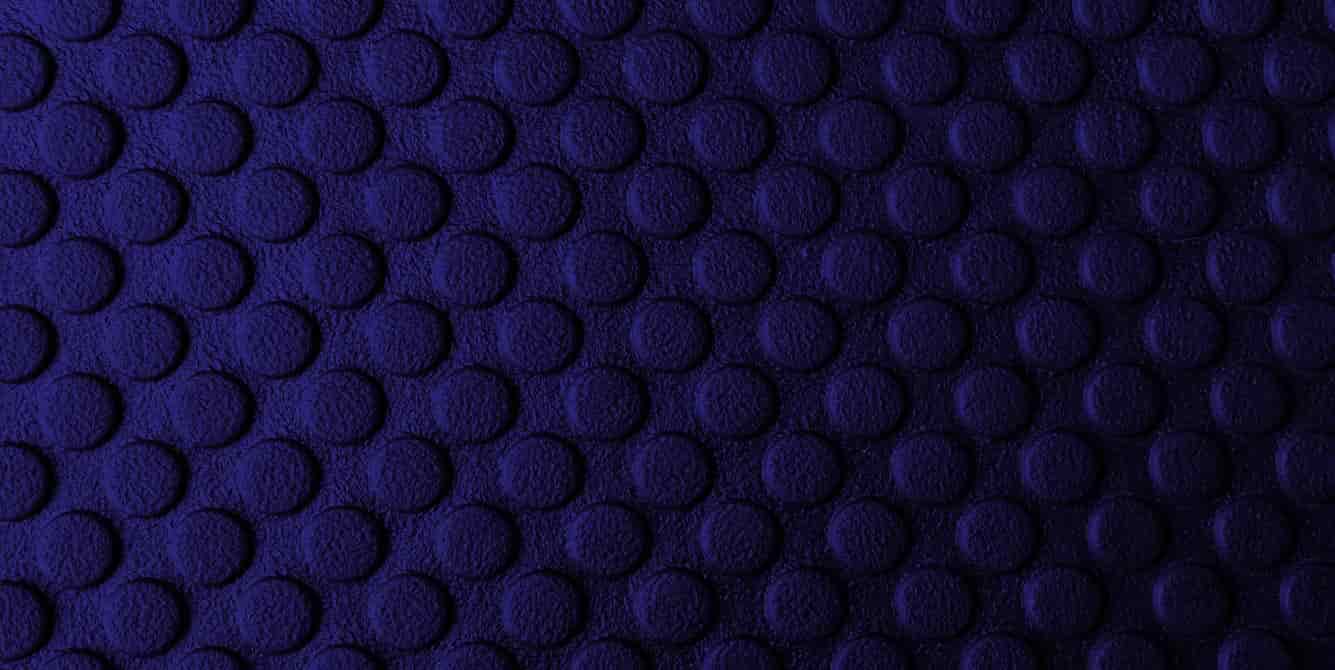
Frequently Asked Questions About Rubber Parts
Please review the following Frequently Asked Questions for a quick answer to your question. The questions are grouped by several categories for easier searching. If you don't find the information you need, please call us at 888-745-7296 or e-mail info@timcorubber.com
Company - General FAQs
- Do you have a direct sales force or do you have manufacturer's reps?
- Timco Rubber employs a direct sales force that covers all regions of the country. We do not sell through manufacturer's representatives.
- Can you provide a catalog of parts you currently supply?
- We do not produce a catalog because we supply custom rubber products made to our customers' drawings or specific to their individual application.
- How long have you been in business?
- Timco Rubber was founded in 1956.
- How big is your company?
- Timco Rubber is a family owned and privately held company. We are small enough to react quickly and provide fast customer service, but large enough to ensure you get the products and service you need every time.
- What is your minimum order size?
- Because all products are custom made, the minimum order will depend on how much the batch of rubber will yield for the part you are requesting.
- Do you supply material?
- We are not a material supplier, however, we might be able to help you with your material needs if they are in sheets or on a roll.
- What do you need for me to establish an account as a customer?
- We need credit references and some general company contact information.
- Where can I get your credit references form?
- Please email us at info@timcorubber.com or click here for a Credit Application.
- How do I get a quote on a product?
- Send your inquiry and drawing to sales@timcorubber.com or visit the Request Quote section of our website.
- What types of rubber parts do you supply (e.g. extruded, molded, etc.)?
- We supply custom molded, extruded, die cut and lathe cut rubber parts, as well as extruded plastics.
- What are the different types of materials available to Timco Rubber?
- We work with a number of different materials, including EPDM, neoprene, silicone, nitrile, butyl, SBR, isoprene (synthetic natural rubber), Viton®, rigid and flexbile PVC, and various types of sponge rubber.
- What are the different markets Timco Rubber serves?
- We work with hundreds of companies across a number of markets, including HVAC, appliance, heavy equipment, power tools, tier 2 automotive, recreation, construction, mass transit, elevator doors, and electrical safety equipment.
- Why does my quotation read, 'Partial tooling charge'?
- Generally speaking, Timco Rubber retains ownership of the tooling quoted. We can quote 100 percent of the tooling costs should you wish to procure ownership of tooling.
- What information do you need to get the most accurate quote possible?
- To get the most accurate quote, you will need to provide: Estimated Annual Usage, Material specs, and a drawing or description of the rubber part.
- When do you lower your prices?
- When rubber compounds have fallen and look to remain in a downward trend to a point that warrants lower part prices, Timco will lower prices. Most likely this happens after a rise in rubber compounds that have resulted in a price increase.
- Why does it take 4-6 weeks for tooling and samples?
- Tooling and sample lead time is 4-6 weeks because the tool must first be produced. There is a trial on a tool and most often there has to be a new tool made or a tweak made to the existing tooling. This might take a couple of times to get the correct part. Once the tool is ready, we then have to run the samples and get all of the supporting documentation prepared and ready to send to you for part approval.
- Do you have material stocked on the shelf?
- No, Timco Rubber does not stock rubber materials on the shelf.
Capabilities FAQs
- Is your company set up to support a KANBAN system?
- Yes we are. We currently provide Kanban services to several of our customers.
- Is your company's quality system ISO certified?
- Proudly, we are. Our certification to ISO standards has been in effect since 1998. Timco Rubber is an ISO 9001:2015 certified company.
- Do you have the ability to do rubber-to-metal bonding?
- Yes. Sizes of custom rubber-to-metal bonded parts we currently supply range from small - less than 1 inch in diameter - to very large - more than 1 foot overall length.
- Can you use our existing tooling in your equipment?
- In some cases, yes. We may be able to use your existing tool depending on several factors, which include type, size and age of the mold. Please make sure to mention you have an existing tool when speaking to your Timco Rubber sales representative.
- Do you stock parts?
- Because the majority of our custom rubber parts are made from customer-owned tooling, we typically do not act as a stocking company. However, we do have some parts that are used more frequently that we might have stocked such as plugs, grommets and some tubing. We can also stock parts specific to your needs, which we currently do for a number of customers. We ship and release per your schedule.
- What is the lead time on a request for quote?
- The lead time for a quote for a molded rubber product is 5 to 7 business days. The lead time for an extruded rubber or die cut part is about 3 to 5 business days.
- What is the lead time for samples and tooling?
- The lead time for tooling and samples is typically 4 to 6 weeks for an extruded sample and 6 to 8 weeks for a mold and samples.
- What is the lead time for production parts?
- Production parts are made based upon approval of the samples. For extruded/die cut production, the lead time is 4 to 5 weeks and molded parts are approximately 5 to 6 weeks for production.
- Do you do PPAPs?
- Yes, we do PPAPs. This information should be communicated to Timco Rubber when the request for quotation is submitted, along with any other information pertinent (i.e., testing) to the form/fit/function of the part.
- Do you work with sponge rubber?
- Yes we work with sponge rubber, both extrusions and molded.
- Do you work with plastics?
- Yes we do work with plastics, both extrusions and molded.
- Do you have offshore contacts?
- Yes, we have several offshore contacts.
- What types of inventory programs do you offer?
- We currently participate in a number of different inventory programs, including Kanban and consignment.
- Can you help determine the appropriate polymer and durometer for my application?
- Yes, our experienced team of experts can guide you in determining the appropriate type of rubber or polymer based on the application and environment your part will be exposed to.
- Can you ship my order direct to my customer(s)?
- Yes, under many circumstances.
- Why do I have to 'sign-off' on these Pre-Production/Sample parts before the production order runs? I need this order ASAP!
- One can waive the right of sample approval, but in doing so you also relinquish subsequent rights to change or correct the part prior to actual production.
- My parts require light assembly. Does Timco offer light assembly on parts or packages?
- Yes, we do offer light assembly on both parts and packages.
- Can I amortize my tooling costs into the piece price for my initial order?
- Yes. Tooling costs can be amortized into the piece price.
- I do not want to purchase tooling, how can I get parts?
- Most parts are going to require new tooling. We might have some rubber parts that are more common and tooling is already available. You would have to speak to our staff to help you through this process.
- What kind of tolerances can you hold on your extruded rubber parts?
- The tolerances of our extruded rubber parts will depend on the specific application. We can quote the appropriate tolerances once the application is determined.
- What kind of tolerances can you hold on your molded rubber parts?
- The tolerances of our molded rubber parts will depend on the specific application. We can quote the appropriate tolerances once the application is determined.
- What kind of tolerances can you hold on your die cut rubber parts?
- Depending on the application we can quote the appropriate tolerances for your die cut rubber part.
- What is the lowest durometer you can process?
- Durometer limits will depend on the type of rubber part that you need:
Extruded parts — 40 durometer
Molded parts — 30 durometer - What is the highest durometer you can process?
- Durometer limits will depend on the type of rubber part that you need:
Extruded parts — 80 durometer
Molded parts — 90 durometer
Technical / Industry FAQs
- I need a particular extruded rubber profile glued or spliced into one continuous piece - much like a doughnut. How strong is seal where the two pieces meet?
- Properly bonded, it will be the strongest portion of the seal or profile.
- What does it mean to be concave when talking about die cut parts?
- When die cutting parts, the material is compressed so it doesn't move. The blade then strikes the material through and then the compression is released. An inward curve is on each side of the cut edge. The concavity becomes more apparent on thicker parts. If this is a problem, parts could be cut using the more expensive water jet method.
- What's so complicated about a washer?
- There are many options to make a rubber washer. A lot depends on the customer's flatness requirements and quantities. If a truly flat both sides part is needed, lathe cutting is a good fit. Depending on the quantities and thickness, you could also die cut the parts from a sheet of material. If the tolerances are less stringent then you could 'throp-cut' the part using a high speed cutter system. Throp cutting is normally used for high volume parts. If there are thicker requirements, you could also use a circular water cooled saw.
- What is an 'accordion-cut' or 'scrunch-cut' gasket?
- To get rid of the 'doughnut-hole' issue, you could explore having a rectangular gasket with a hole in the middle cut so that it could be nearly cut through on the 45 degree ends of the 'picture frame' and then assembled into the rectangular shape. The scrap material in the middle of the part would be eliminated and the cost savings could be passed on to the customer.
- What do you mean by 'Intermittent temperature'?
- When higher or lower temperature requirements are needed for parts, you may see this term used. An example would be standard silicone meeting 450 degrees F for constant usage, but it could reach 500 degrees F for intermittent usage. In any case, make sure to declare your temperature requirements when talking about your application.
- Will butyl rubber deaden more vibration than other compounds?
- Yes.
- How do I reduce/eliminate the tackiness of a surface having adhesive on it?
- Use a light dusting of talc.
- How do I help install a rubber part in or over a metal?
- Use a 50/50 mixture of a dishwashing liquid and water. After the soapy water dries, there may only be a harmless soap coating left. Do not use an oil or hydrocarbon as the rubber may swell.
- What is kiss cutting?
- A kiss-cut part is a sheet of die cut parts with pressure sensitive adhesive on at least one side. The rubber material is cut and so is the adhesive attached to it. The backing paper it is on is not cut through. The die cut part with its adhesive is then lifted off the backer paper for use.
- Who is the RMA?
- The Rubber Manufacturers Association (RMA) is the national trade association representing the finished elastomeric products industry in the United States. The association's membership is recognized for its standards in regard to tolerances for fit and finish of parts.
- What is mandrel forming?
- Mandrel forming parts is a multi-step process. Usually a steel rod having the same OD as the ID of the finished rubber part is bent into the configuration of the desired part. Uncured rubber with an ID similar to that of the OD of the steel mandrel is extruded and cut to a somewhat longer length than the end part. The uncured rubber hose is put over the steel mandrel and then cured in an autoclave (cure-time). Parts are then removed from the mandrel, cleaned from the mold release agent, and then trimmed to length.
Quality at Timco Rubber FAQs
- Can Timco Rubber trace parts back to the raw material supplier?
- Yes, a blue lot label is put on each carton. This lot number traces the material back to the raw material supplier.
- Do you track cost of quality?
- Yes, our goal is to have a cost of quality below 2%.
- How long are quality records maintained?
- A minimum of three years.
- Do records indicate that gauging and test equipment are periodically inspected and traceable to N.I.S.T.?
- Yes, gauges are calibrated annually and semi-annually according to the calibration schedule and traceable to N.I.S.T.
- Does Timco Rubber utilize FIFO?
- Yes.
- How are suppliers monitored?
- Suppliers are rated quarterly on their performance. This information is used to improve our suppliers' performance and recognize suppliers who are meeting our quality requirements.
- What are Timco Rubber's strengths?
- Timco Rubber focuses on meeting the most demanding specifications of your rubber applications while ensuring the highest level of quality, customer service and on-time delivery at a competitive price.
- Do you have a continuous improvement procedure?
- Yes, we have a written procedure and form for all continuous improvement projects. We deploy a continuous improvement philosophy throughout the entire organization. Everyone is encouraged to come forward with ideas for improving products, processes, systems, productivity and the working environment. Techniques include control charts, theory of constraints, parts per million analysis, FMEAs, value analysis, etc.
- How often does the management team review the effectiveness of the quality system?
- Semi-annual quality meetings are conducted along with monthly staff meetings, quarterly sales meetings, strategic business meetings and weekly production meetings. Monthly internal audits are another method we use to review the effectiveness of the quality system. Any non-conformances are addressed immediately through corrective action.
- Are training needs defined for all employees?
- Yes, employees are reviewed quarterly and training effectiveness is reviewed at that time. We maintain records of training electronically. Cross-training is conducted as needed and full-time employees are required to have a minimum of 20 hours of training per year.
- Are holding areas for non-conforming material available and used?
- Yes, we place parts in the hold area and red-tag them per our procedures.
- Does Timco Rubber have a formal corrective action program in place?
- Yes, our quality manager initiates the corrective action. If our supplier is responsible for the root cause, a corrective action is issued to our supplier per our procedure.
- Do you have a preventive action system to determine and prevent potential nonconformities?
- Yes, per our procedure. Some of the sources used for determining preventive action include, but are not limited to, analysis of statistical data, corrective actions, non-conformance reports and customer surveys.