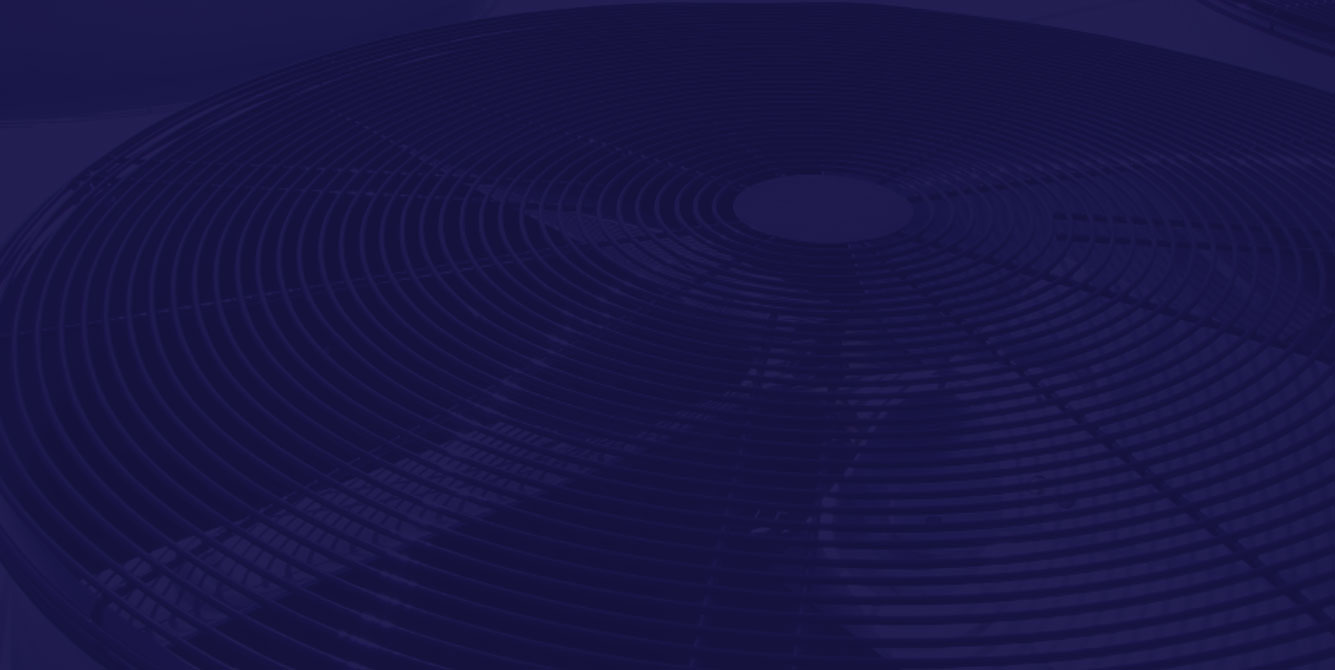
Sponge & Foam Rubber Manufacturer
Seals, Tubing & Gaskets & More
Whether you call it foam rubber or sponge rubber, it's important to get the perfect parts for your applications. Timco Rubber works with companies to provides them with custom rubber products that offer cost-effective sealing and cushioning solutions for your applications.
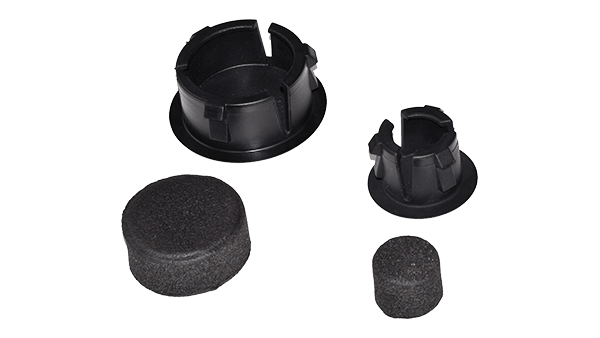
Custom Foam & Sponge Rubber Solutions for Your Business
While the terms foam and sponge are used interchangeably, they aren’t quite the same material. Both foam and sponge have cellular structures, but each option has various features that may make one a better choice for your needs.
A major difference between the two is the open and closed structures of the two materials. Flexible foam rubber (also known as cellular or expanded rubber) has an open cell structure and can be produced in low and high densities, making it ideal for seals and insulation for cabinet and commercial applications. Sponge rubber has a much more closed cell structure that provides strong compression set resistance and compression recovery, along with the ability to block liquids and gases.
No matter whether you need EPDM foam rubber tubing or sponge rubber vibration isolators, Timco can work with your business to customize a part solution based on your specific needs and budget.
Types of Foam Rubber
Cross-Linked Polyethylene Foam
- Compact
- Water-resistant
- Offers cushioning and support
- More resistance and spring back
Polyurethane Foam
- Lightweight
- Easy to work with
- More cost-effective than other foam options on the market
Microcellular Urethane Foam
- Low compression set
- Excellent durability
- Resistant to abrasion
- Good for open and close applications with repetitive access
Foam Applications
- Dust seals for HVAC access doors
- Foam rubber insulation
- Noise and vibration reducers
- Transportation
- Automotive trim
- Refrigerated transport vehicles
- Foam rubber tubes
- Foam rubber seals
Foam Benefits and Advantages
- Lightweight materials
- Buoyant
- A range of compressibility available
- Excellent cushioning and impact deadening performance
- Thermal and acoustical insulation
- Cost effective compared to other materials
- Can be produce in low and high densities
Types of Sponge Rubber
EPDM Sponge Rubber
- Excellent resisting aging from weather and sunlight
- Withstands adverse outdoor conditions better than neoprene
- Requires proper additive to meet UL flame ratings
- Vulnerable to oils and fuels
Silicone Sponge Rubber
- High temperature stability
- Temperature usage exposure from -100°F up to 500°F
- Strong levels of resilience
- Less flame resistant, usually can't achieve flame ratings beyond UL94HB
- Resists degradation and aging due to sunlight and ozone exposure
PVC/Nitrile Sponge Rubber
- Great thermal conductivity
- Excellent oil and fluid resistance
- Excellent for shock absorption and padding
- Provides gas and air impermeability
Sponge Rubber Applications
- HVAC Market
- Sound and vibration insulation
- Seals for doors, cabinets, etc.
- HVAC & Automotive Markets
- Sound dampening
- Sponge gaskets
- Fabricating processes available for all materials include:
- Die cutting
- Slitting to width
- Adhesive lamination
Sponge Benefits & Advantages
- Highly effective sealing capabilities
- Can be specified in low, medium or high-density firmness
- Controlled compression and recovery characteristics
- Shock absorption attributes
Foam/Sponge Rubber FAQs
Q: What is foam and sponger rubber?
A: Foam rubber, which is sometimes interchangeably known as sponge rubber, is a type of rubber that has a porous, cellular structure. The main difference is that foam rubber has a more open cell structure, while sponge rubber is more closed. These structures are created by incorporating gas bubbles into the rubber during the manufacturing process, resulting in a lightweight, flexible material with excellent cushioning properties.
Q: What are the primary characteristics of foam/sponge rubber?
A: Foam/sponge rubber is known for several key characteristics:
- Lightweight: Due to its cellular structure, it is significantly lighter than solid rubber.
- Compression Set Resistance: It has a good ability to recover and retain shape after being compressed.
- Cushioning and Shock Absorption: It offers excellent energy absorption, making it ideal for padding and insulation applications.
- Thermal Insulation: The foam structure also provides good insulation against heat and sound.
- Flexibility and Softness: It is highly flexible and soft to the touch, providing comfort in many applications.
Q: What are some common types of foam/sponge rubber?
A: There are various types of foam/sponge rubber, each designed for specific applications:
- Cross-Linked Polyethylene Foam: A compact material that resists water and offers excellent cushioning.
- Polyurethane Foam: An extremely lightweight rubber that is highly regarded as a cost-effective material that is easy to work with.
- Microcellular Urethane Foam: An extremely durable rubber that resists abrasion and is ideal for applications that open and close regularly.
- EPDM Sponge: A rubber that resists weathering and adverse outdoor conditions.
- Silicone Sponge: A high-temperature sponge rubber that also excels outdoors.
- PVC/Nitrile Sponge: A sponge rubber designed for use around oils, shock absorption, and impermeability.
Q: What are the common applications of foam/sponge rubber?
A: Foam/sponge rubber is used in a wide range of industries, including:
- Automotive and Transportation: Trims, gaskets, seals, vibration dampening, and soundproofing materials.
- Construction: Insulation, access door seals.
- HVAC: Access seals, insulation, gaskets, and dampeners.
- Medical: Cushions and padding for medical devices, patient care, and prosthetics.
Q: How is foam/sponge rubber made?
A: Foam/sponge rubber is typically made by incorporating a foaming agent into the rubber compound. During the manufacturing process, heat is applied to create gas bubbles within the rubber, which form the cell structure. The rubber is then cured or vulcanized to achieve the desired properties.
Q: What are the benefits of using foam/sponge rubber?
A: Foam/sponge rubber offers several benefits:
- Cost-Effective: It is often more affordable than solid rubber due to its lightweight and material-efficient structure.
- Versatility: Available in a range of densities and hardness levels, it can be customized for different applications.
- Comfort and Cushioning: Its softness and ability to absorb shock make it ideal for comfort-related applications such as padding and mattresses.
- Sound and Vibration Dampening: Its cellular structure effectively reduces noise and vibrations, making it useful in automotive, construction, and industrial settings.
Q: What are the limitations of foam/sponge rubber?
A: While synthetic rubber is versatile, it does have some limitations:
- Durability Issues: It may be less durable than solid rubber in high-stress or abrasive environments.
- Limited Chemical Resistance: Certain types of foam rubber may not perform well when exposed to harsh chemicals, oils, or fuels.
- Water Absorption (Open-Cell Foam): Open-cell foam can absorb moisture, which may lead to mold or mildew growth over time in damp environments.
- Compression Set: While it resists compression well, excessive or prolonged compression can cause permanent deformation, especially in low-density foams.
Q: How are foam/sponge rubber products processed and formed?
A: Foam/sponge rubber is processed through several methods:
- Extrusion: Used to create continuous shapes such as strips or profiles, which can be cut to specific lengths for various applications.
- Molding: Poured into molds to create complex shapes as needed for a design.
- Calendering: This method is used to produce thin sheets and films that can be cut into smaller pieces or strips, often for insulation or coating applications.
- Lamination and Bonding: Layers of foam can be bonded together or to other materials for specific applications like cushioning or insulation.
Q: Can foam/sponge rubber be customized?
A: Yes, foam/sponge rubber can be customized in a variety of ways, including:
- Density: Varies from soft and flexible to firm and supportive, depending on the application.
- Thickness: Available in a wide range of thicknesses to suit different cushioning and insulation needs.
- Foam Type: Custom formulations can be developed for specific resistance to heat, chemicals, or oils.
- Surface Texture: The surface of foam rubber can be textured or smooth, depending on the end-use requirements.
Interested in foam rubber and sponge rubber parts?
Call 1-888-754-5136 to find out more, or get a quote.
Not sure which material you need for your custom rubber product? View our rubber material selection guide.
Want to make sure that Timco is the right partner for all your foam and sponge rubber part requirements?