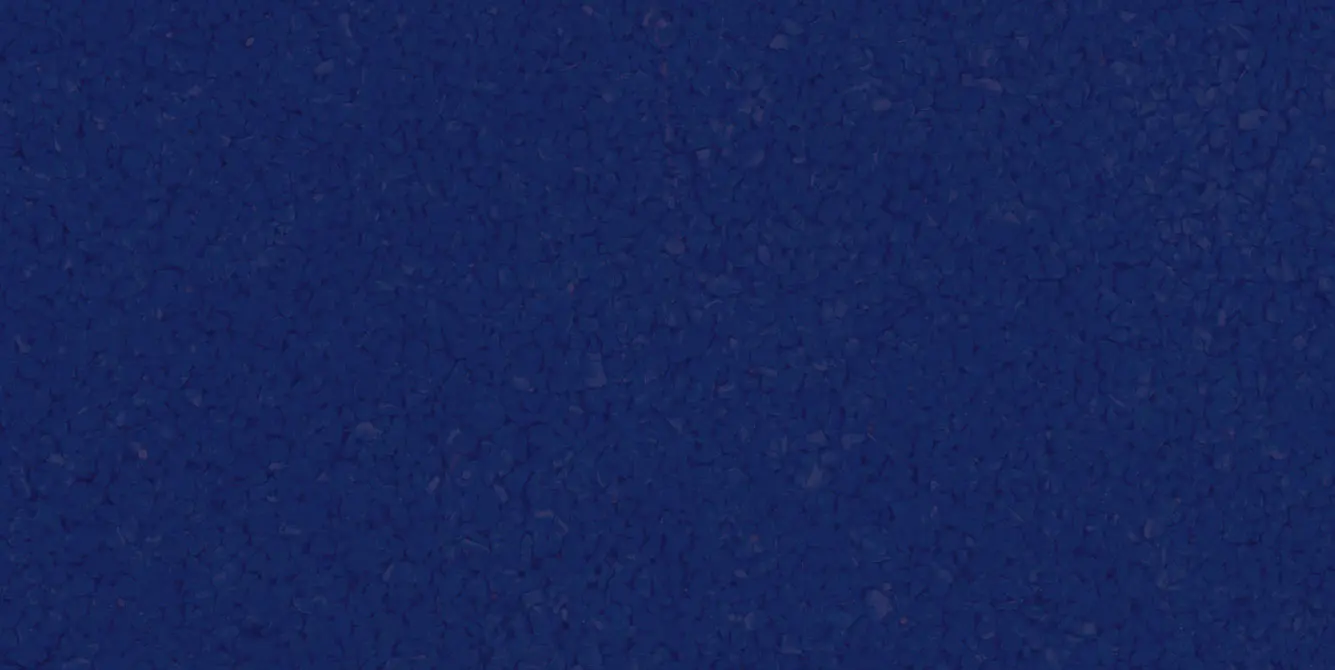
EPDM Rubber Material Manufacturer & Supplier
Gaskets, Seals, Grommets & More
EPDM rubber is a high-density synthetic rubber used for outdoor applications and other spaces in need of tough, versatile parts. With more than half a decade of experience in providing custom rubber solutions for businesses, Timco Rubber can work with you to provide the right EPDM parts for your applications.
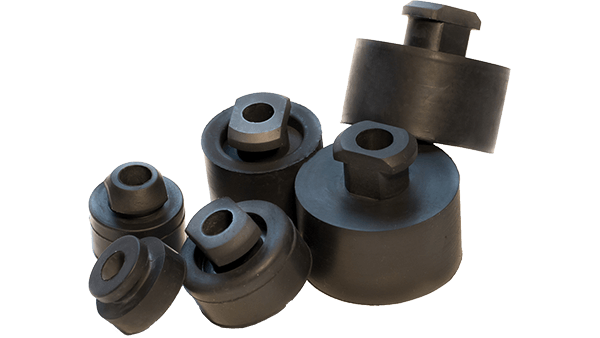
What is EPDM: A Versatile, Cost-Effective Rubber Part Solution
When you need a rubber material that offers excellent resistances to weather, heat, and other factors without breaking the bank, EPDM grommets, gaskets, tubing, and other parts may be the answer you need.
EPDM – also known as ethylene propylene diene monomer – is an extremely versatile material used in a variety of applications, from automotive products to HVAC parts. This type of rubber also acts as a less expensive alternative to silicone, as it can endure weather conditions, abrasion, and other challenges for long periods of time with proper use.
Due to its combination of physical durability, performance capabilities, and cost, investing in custom EPDM parts can save you time and money on a wide range of applications. These benefits have made EPDM a go-to material for many parts.
What Does EPDM Rubber Come From?
EPDM is a synthetic rubber derived from the polymerization of ethylene, propylene, and certain other alpha-olefin comonomers. The first example of EPDM dates back to Nobel Prize winner Karl Ziegler.
The German scientist discovered that he could product a strong, flexible compound while conducting polymerization experiments. The new material was first introduced to the U.S. market in the early ‘60s, quickly gaining popularity in the roofing and other industries for it’s beneficial properties and cost-effective price point.
One of the major reasons why EPDM caught on as a rubber compound was because it marked the first elastomer developed that combined good heat resistance, ozone resistance, excellent mechanical properties over a wide temperature range, and good chemical stability. While other materials have been created to address greater temperature needs and other performance factors, EPDM has maintained popularity and is ideal for many uses.
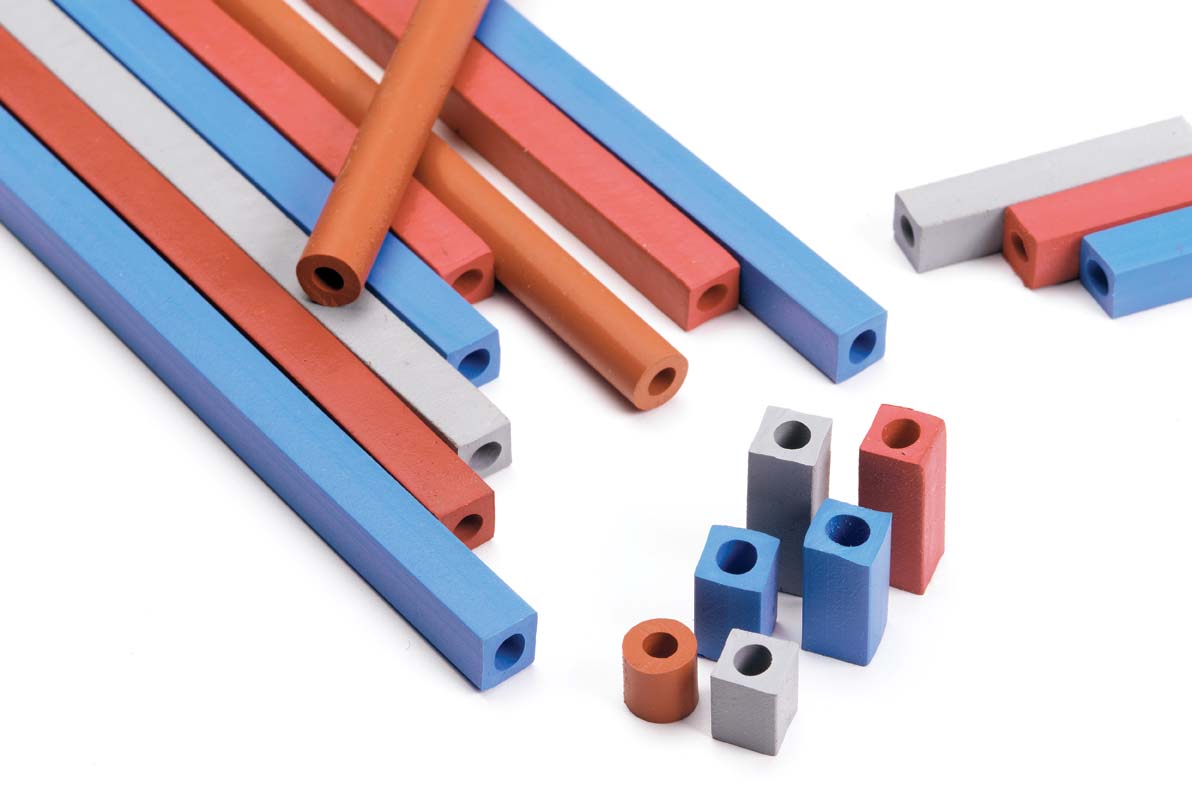
EPDM Properties
- Common Name: EPDM
- ASTM D-2000 Classification: CA
- Chemical Definition: Ethylene Propylene Diene Monomer
- Temperature Range
- Low Temperature Usage:-20° to -60° F | -29⁰C to -51⁰C
- High Temperature Usage: Up to 350° F | Up to 177⁰C
- Tensile Strength
- Tensile Range: 500-2500 P.S.I.
- Elongation: 600% Maximum
- Durometer (Hardness) – Range: 30-90 Shore A
- Resistances
- Aging Weather - Sunlight: Excellent
- Abrasion Resistance: Good
- Tear Resistance: Fair
- Solvent Resistance: Poor
- Oil Resistance: Poor
- General Characteristics
- Adhesion to Metals: Fair to Good
- Solvent Resistance: Poor
- Compression Set: Good
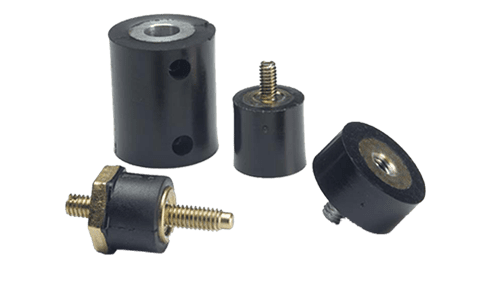
EPDM Applications
Thanks to its versatility and cost-effectiveness, EPDM is used in a wide variety of markets. Common industries and applications include:
HVAC
- Compressor grommets
- Mandrel formed drain tubes
- Pressure switch tubing
- Panel gaskets and seals
Automotive
- Weather stripping and seals
- Wire and cable harnesses
- Window spacers
- Hydraulic brake systems
- Door, window, and trunk seals
Industrial
- Water system O-rings and hoses
- Tubing
- Grommets
- Belts
- Electrical insulation and stinger covers
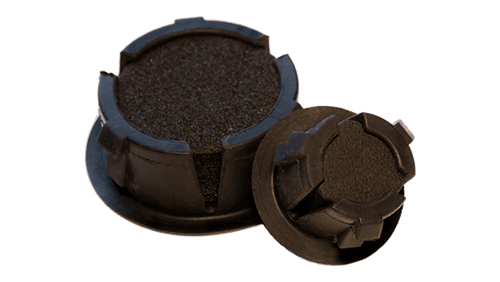
EPDM Benefits and Advantages
- Resistance to UV exposure, ozone, aging, weathering, and many chemicals – great for outdoor applications.
- Stability in high and low temperatures – a general purpose EPDM material can be used in an environment where the temperature range is from -20⁰F to +350⁰F (-29⁰C to 177⁰C).
- Offers excellent resistance to highly acidic substances and corrosive materials, making it ideal for parts that encounter intermittent or even regular exposure to caustic elements.
- Features low toxicity and odor levels, making EDPM rubber a safer option for applications meant for human interaction.
- Low electrical conductivity.
- Steam and water resistant.
- Can be fabricated in a variety of ways, which includes custom molding, extruding, sheeting, and die cutting.
- Long-term part lifespan allows for fewer replacement parts, saving money in the long run.
Timco: Your Go-To Supplier of EPDM Parts
EPDM rubber parts are built to last, but it takes the right solutions to help you address your specific design needs and budget. EPDM can be manufactured a lot of different ways, which is why Timco partners with businesses to help them invest in custom EPDM parts tailored specifically to their performance criteria and budget.
Our goal is simple – to deliver high quality parts and customer service. Our experts work with you to analyze your needs and deliver a custom-designed part solution based on your goals. In addition to supplying custom EPDM parts, we also offer the following value-added services to help you save valuable time and money:
- Subassembly of rubber parts
- Kanban replenishment
- Kit assembly
- Flexible control methods
- Our in-house stocking program and on-time delivery
Want to make sure that Timco is the right partner for all your EPDM part requirements?
EPDM Rubber FAQs
Q: What is EPDM rubber and what are its primary uses?
EPDM rubber is a type of synthetic rubber known for its excellent resistance to weathering, ozone, and various chemicals. It's commonly used in seals, gaskets, hoses, and other parts for a wide range of industries.
Q: What are the key properties of EPDM rubber?
EPDM offers outstanding flexibility, durability, and resistance to UV rays, ozone, water, and heat. It also has good electrical insulating properties and can withstand a fairly wide temperature range.
Q: How does EPDM rubber compare to other types of rubber like silicone or neoprene?
EPDM is generally more cost-effective and offers better resistance to weathering and ozone compared to silicone, but doesn’t match silicone when it comes to temperature resistance. Neoprene provides better oil resistance, whereas EPDM excels in applications requiring excellent weather and water resistance.
Q: What are the advantages and disadvantages of using EPDM rubber?
- Advantages:
- Superior weather and ozone resistance
- Flexibility and stability over a wide temperature range
- Able to be manufactured in a variety of ways
- Cost-effective
- Disadvantages:
- Poor resistance to oils and some chemicals
- Can be prone to issues with tearing compared to other rubbers
Q: Is EPDM rubber waterproof and suitable for outdoor use?
EPDM is highly water resistant and is specifically designed to withstand outdoor conditions, including exposure to rain, sunlight, and temperature fluctuations.
Q: What is the typical lifespan of EPDM rubber products?
When properly installed and maintained, EPDM rubber products can last up to 15 years, with some parts lasting more than 50 years depending on working conditions. As with other materials, exposure to oil and other adverse substances can cause EPDM to degrade quicker than expected.
Q: How should EPDM rubber be maintained to ensure longevity?
Regular inspections for signs of wear or damage, cleaning with mild detergents, avoiding exposure to harsh chemicals, and prompt repair of tears and other damage can help extend the lifespan of EPDM rubber depending on the part.
Q: What are the common applications of EPDM rubber in the automotive industry?
EPDM is used in windshield seals, door seals, radiator hoses, belts, gaskets, and various other components that require flexibility and resistance to heat and weathering
Q: Can neoprene rubber be recycled, and if so, how?
Yes, EPDM can be recycled at an appropriate facility. Recycling processes typically involve grinding the rubber into smaller particles, which can then be reused in products like mats, playground surfaces, and other rubber goods. Some facilities specialize in chemical recycling, breaking down EPDM into its constituent monomers for repolymerization.
Interested in EPDM Gaskets, Grommets, and other Parts?
Call 1-888-918-5351 or complete our online form to request a quote.
EPDM Case Study: Switch to Square Tubing Saves Money and Improves Quality
Not sure which material you need for your custom rubber product? View our rubber material selection guide.