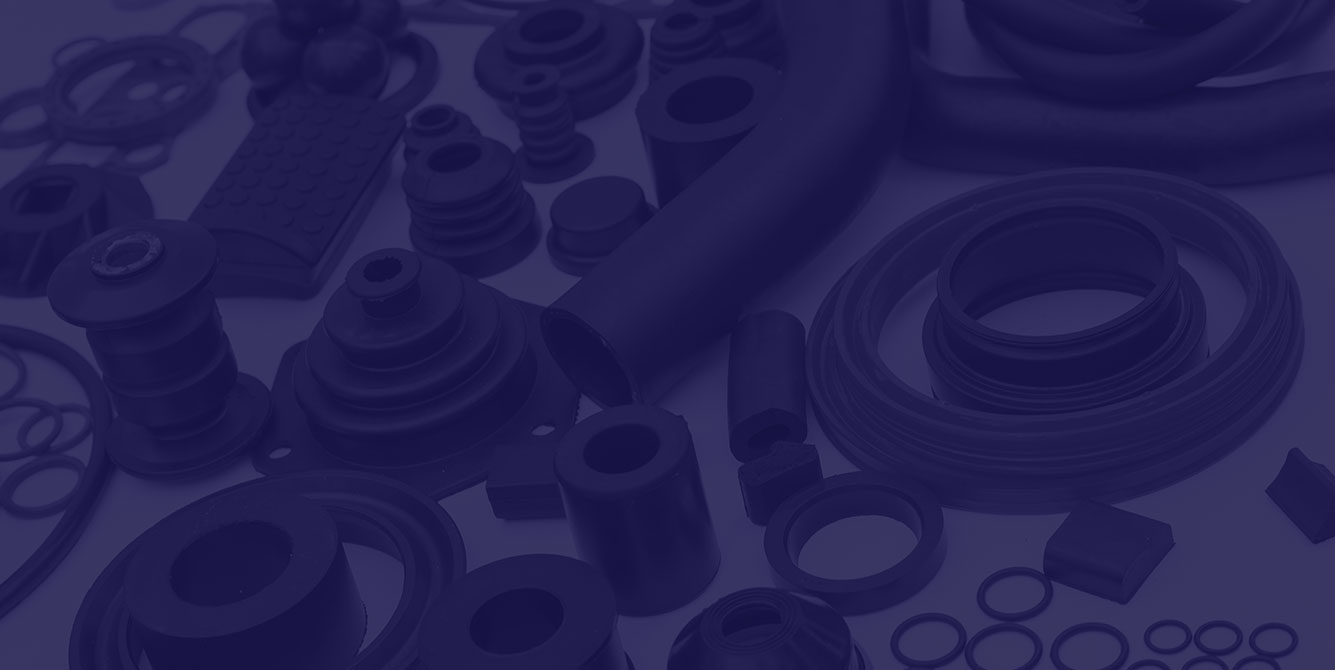
Conditional Differentiation in Extruded Rubber… Why?
Switch to square tubing saves money and improves quality
Switch to square tubing saves money and improves quality
The most common method of running extrusions is to feed a raw, pliable and uncured rubber compound through a screw machine. This material is then compressed as it follows the winding twines. In the process, it heats up. It is forced under significant pressure through the die. As it exits the die orifice in the desired shape or profile, the rubber typically swells.
Ever wonder what the weather conditions are like in a non-environmentally controlled factory where most extrusions come from? It could be 93 degrees with a humidity level of 85 percent for several days. Then it could be 68 degrees with a humidity level of 20 percent the next month. Or, somewhere in between. Although slight, these variables do impact the degree of swelling or cross-sectional shrinkage the uncured rubber undergoes.
Variables in the vulcanization or curing process of the rubber also play a large factor. The temperature of heat used, the length of time exposed in that heat, line speed as the rubber proceeds down the line and the degree of stabilization used for any given extrusion shape will affect the outcome of the rubber product.
The most common types of vulcanization (or curing of the raw rubber) processes include (steam) heating in a pressure vessel known as an autoclave, microwaving in an enclosed cavity and submersion in heated salt baths. Each has variables of their own, as mentioned above. As such, these conditions along with the very nature of rubber itself - having a great deal of load-deflection characteristics - account for greater tolerances in receiving finished extruded rubber parts.