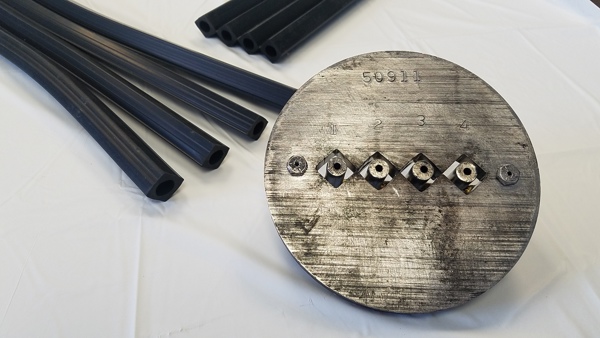
Not all custom rubber parts are made the same way. There are different processes that companies use to manufacture these parts depending on the specific design or needs. Certain qualities, such as overall size and a level of intricacy, can help us determine which manufacturing process is right for your custom rubber parts.
Of course, the process also impacts the price. The tooling costs for extruded parts and molded parts can be quite different, which in turn affects the quotes for your rubber parts. This is due to the level of time, labor, and detail involved with both processes.
The Differences Between Extruding and Molding Rubber
There’s a wide gap between the tooling costs for extruded and molded parts. In short, extrusion tooling costs are much less expensive than those for molding. To understand why tooling costs can differ by so much calls for a quick examination of how each process works.
Extrusions
To understand how extrusion works, all you need is some Play-Doh. As a kid, you could take some Play-Doh and place it in a little machine. You could then push down on a lever or turn a crank that would push the Play-Doh through a specially-shaped attachment at the end to create elongated pieces of Play-Doh. Extrusion operates in the same way, except that you replace the Play-Doh with rubber and the equipment with industrial extruders and custom-extrusion dies.
Extruders take raw rubber and concentrates it under pressure and heat. The rubber is then ejected through a customized die to form whatever shape you need for your part. From there, these parts are cured and cut to length to create final parts. You can also put the pieces in an autoclave under heat pressure to cure it to create vulcanized rubber parts.
The extrusion process is much simpler than molding for a few reasons. First, it’s designed to create long pieces of rubber that are typically no more than 15 inches wide and can be cut into single pieces with a band saw or some other standard device. Second, the dies used to shape these long pieces aren’t nearly as complex as those used for molding. Extrusion dies are typically made of one or two pieces and don’t require as much metal or detail that would make for more expensive tooling costs.
Molds
The main reason why tooling costs for molded rubber is more expensive than the extrusion process is that it requires manufacturers to invest in a special mold made for your specific part. To make your parts, rubber is injected into the holes of a mold. The rubber is subjected to both pressure and heat over time until it forms into specific parts. The mold is then opened to eject the newly-formed pieces before the process starts over again.
This process allows you to make custom rubber parts that are either too big or too complicated for an extruder. However, the need for a custom-made mold also adds significantly to the tooling costs. These molds require a large, solid piece of steel, cut it in half, and carve a detailed cavity into it that matches the part’s design. Cutting and carving hardened metal is difficult, especially when there’s little room for error. Certain factors can impact the overall cost, such as which metal is used to make the mold, but it will be more expensive than an extrusion die that fits on the end of an extruder.
Custom Rubber Parts
Tooling costs are a necessary part of creating custom rubber parts, but it’s still important to try and make extrusion dies and custom molds as economical as possible. At Timco, we work with you to weigh certain factors such as usage estimation to try and drive down any potential tooling costs and determine the most cost-effective solution for your custom rubber parts.
Contact us today if you have any questions about custom rubber parts or request a quote to submit information on the parts you need for your project.