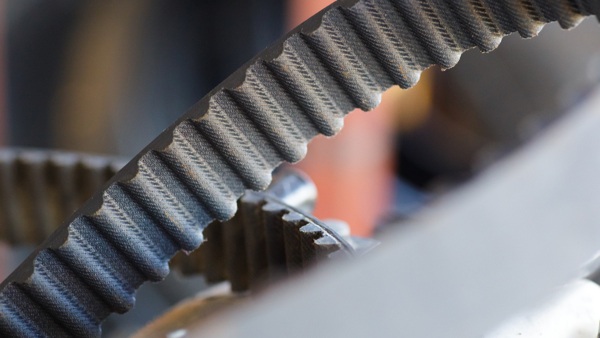
While some rubber parts may never come in physical contact with other surfaces, others will be put to the test. Abrasion resistance is a must for everything from rubber linings to shock mounts, and the right material can make all the difference. Keep reading to learn more about abrasion resistant rubbers and which materials may be suited for your parts.
How is the Abrasion Resistance of Rubber Tested?
The best way to see just how well rubber materials will hold up to regular abrasion is to see how long it lasts under constant scrapes and scuffs. The standard process for test abrasion resistance is to see how well a specific rubber performs in the revolving drum test.
This particular test takes a rubber sample and moves it across an abrasive sheet mounted to a drum. As the drum revolves, the regular abrasion will attempt to wear down the test rubber. After a set period of time, the drum will stop and someone will remove and weigh the rubber sample.
The amount of weight and volume lost during this process will signify the abrasion resistance of a material. Samples the lose less weight and volume were better able to withstand scuffs and scrapes, whereas samples that lost more weight weren’t able to resist the abrasive contact.
Which Rubber Materials are Suited for Abrasion Resistance?
The good news for businesses in need of abrasion resistant rubbers is that there are multiple materials available that can handle regular wear. Let’s break down some common high abrasion rubber materials (and a few you may want to avoid).
High Abrasion Rubbers
Neoprene
Neoprene is multipurpose elastomer for a good reason – it can withstand a lot of challenges. That durability includes excellent abrasion resistance, along with good weathering resistance and solid oil resistance. When it comes to abrasion, the only downside of Neoprene is that it’s so versatile that you might be able to find a more cost-effective alternative.
Nitrile
A lot of what you can say about Neoprene also applies to Nitrile. Both materials share excellent abrasion resistance and the ability to thrive in environments with oil. The major differences are that Nitrile struggles with weathering and sunlight, but can survive even more exposure to oil. Either way both Neoprene and Nitrile aren’t going to let you down when it comes to abrasion.
Natural Rubber
While many applications call for synthetic rubbers, natural rubber is a great option for physically demanding applications. Natural rubber parts can regularly take a beating, making them ideal for agitators, rollers, and other parts – just don’t ask them to last outdoors or in environments with oils or solvents.
Viton
Viton was originally made to last in outer space, so demanding environments are no challenge for this material. This fluoroelastomer polymer can withstand abrasion, tearing, oils, solvents, weathering, and just about everything you can throw at it. Of course, that may make Viton overqualified for your application if you’re looking for more cost-effective materials.
EPDM
EPDM, more formally known as Ethylene Propylene Diene Monomer, is an extremely versatile, cost-effective rubber materials. EPDM offers good resistance to abrasion, weathering, and other long-term challenges, making it a very durable part. Oils and solvents and one of the few drawbacks to using EPDM, so keep that in mind if either of those are present in your application.
Low Abrasion Rubbers
Silicone
Silicone is mostly known as an excellent high-temperature rubber, but it can struggle with more physically demanding applications. Formulations of silicone will provide fair to poor abrasion resistance, making it a less optimal choice if regular wear and tear is a major factor.
Butyl
Butyl is well-regarded for its durability and shock absorption, but it can struggle with abrasion. This material is great for manufacturing shock mounts and liners, but scratching and scraping will wear Butyl down quicker than other available rubbers.
Invest in the Right Abrasion Resistant Parts
The right material can make all the difference. While abrasion can be a major consideration, it’s critical to invest in a material that addresses all your needs.
Fortunately, Timco is here to help businesses identify the best, most cost-effective parts for their performance criteria and budget. Give us a call at 800-969-6242 or contact us online to have one of our experts design and supply the right parts for your applications.