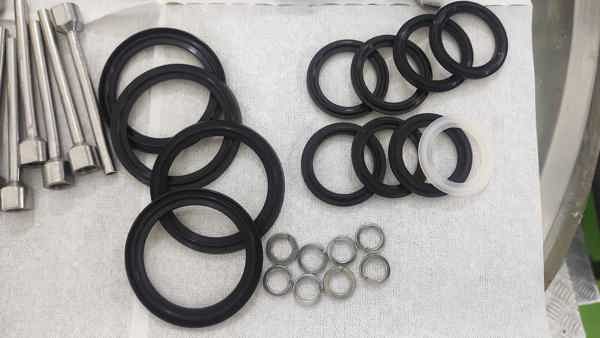
Choosing the right material for your applications isn’t easy. There are several rubbers and compounds available for manufacturing parts, and each of them have different characteristics that can make them viable or not.
Viton and silicone rubber are two notable compounds that are commonly used for demanding environments. Let’s break down some of the key qualities for these two rubber materials to see which is a better fit for your parts.
The Differences Between Viton and Silicone
Both Viton and silicone are both synthetic rubbers, with silicone dating all the way back to the 1800s. Silicone grew in popularity in the early 20th century as a versatile elastomer used in home appliances, automotive applications, and many other markets.
Viton isn’t quite as recognizable to the average person, but it has a well-earned rotation for being a dependable material for environments that would be too much for other rubbers and plastics. Viton is a specific fluoroelastomer polymer (FKM) invented in the 1950s and was originally intended for use in the aerospace industry. Its impressive durability has made it a popular choice for businesses in need of a high-performance elastomer.
While both materials are effective in the right situations, there are specific times when one is more effective than the other. Some of the key differences between Viton and silicone include:
- Temperature ranges
- Elongation
- Fuel and oil compatibility
- Abrasion and tear resistance
- Cost
Temperature ranges
While some materials can’t stand the heat, both silicone and Viton are exceptional at surviving hot environments. Viton does have an edge when it comes to extreme heat resistance, with a top-end range of 600 degrees Fahrenheit.
However, silicone does have an edge when it comes to colder environments. Silicone has an excellent low-end range as low as -150 degrees, which is notably lower than Viton and many other materials.
- Silicone: -150 to 480° F
- Viton: -10 to 600°F
Elongation
Another main difference between these materials lies in how much they can stretch before breaking. Silicone excels at this, with a maximum elongation of 700%. Viton’s max elongation is less than half of silicone, as it can stretch up to three times its original length.
Fuel and oil compatibility
Contact with fuel and oil can quickly break down various rubber and plastic materials. Viton is an exception to this problem. Viton is one of the best materials for oil and petroleum resistance, even in environments with regular exposure. Silicone does offer some minor resistance with less exposure, but it can struggle if oil and fuel are a common concern.
Abrasion and tear resistance
When you need a more physically durable material, Viton is likely a better option. Viton is better at handling abrasion and tearing – no surprise for a material that was originally designed to survive in outer space. Silicone isn’t nearly as capable when it comes to physical duress, so keep the impact of wear and tear in mind if that’s a major factor.
Cost
When materials share a lot of characteristics, your decision often comes down to which one is right for both your parts and your budget. Viton is an incredibly high-performance elastomer, but it also costs more than most rubber and plastic materials due to its ability to perform in extremely difficult environments.
Silicone is also a high-performance material but can be less costly compared to Viton. As a result, it can be a better fit for your parts if Viton or a more expensive material is overqualified for your application. However, that added cost can be well worth the investment if your performance requirements demand it.
Invest in Quality Viton and Silicone Parts That are Right for Your Business
Identifying the right material requires a delicate balancing act to address several pain points, and it isn’t easy to determine which compound is best suited for your performance requirements and budget. Fortunately, a little expertise goes a long way toward deciding which material is right for your applications.
Timco works closely with businesses to provide custom part solutions tailored to their specific needs. We work closely with you to provide part solutions that address the specifications of your unique application. Give us a call at 800-969-6242 or contact us online to have Timco supply your business with the parts you need for your applications.