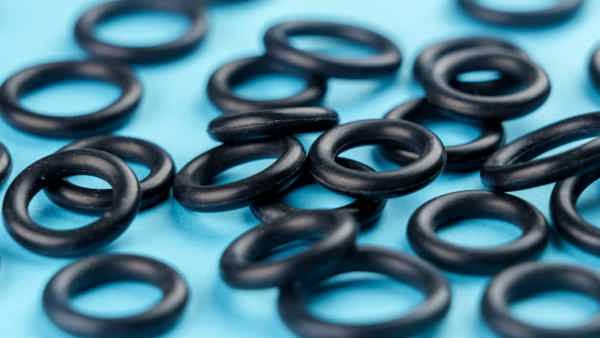
There are several types of synthetic rubbers and plastics available, but only the right materials make sense for your parts. The challenge is that it can be difficult to decide which ones are best for your specific requirements.
TPE and nitrile are a pair of performance materials that can be great fits for your parts depending on your performance needs. Let’s break down some of the main differences between TPE and nitrile rubber to see which is a better fit for your parts.
The Differences Between TPE and Nitrile (NBR)
The biggest difference between TPE and nitrile is simple – one is a performance plastic, and the other is a rubber. TPE, also known as thermoplastic elastomers, became commercially available in the 1950s and now comes in a variety of compounds made to combine advantages found in both plastic and rubber materials.
Nitrile, also known as Nitrile Butadiene Rubber (NBR) and Buna-N, is a synthetic rubber made through the polymerization of acrylonitrile (ACN) and butadiene. This polymerized material is formed into sheets and vulcanized to create different formulations based on desired characteristics.
As with most materials, the most important difference between the two comes down to the benefits and advantages of using them. Both TPE and Nitrile are great sealing solutions and can be manufactured in a variety of ways, but different environmental factors and performance requirements can make one material a better fit. These different needs include:
- Weathering
- Oil resistance
- Use for consumer goods
- Compression set
Weathering
Some parts fare better outdoors than others, and TPE is one of them. TPE ages extremely well when exposed to the sun and other forms of weathering, making it ideal for parts that will be left outside.
Nitrile doesn’t quite fare as well with direct exposure to UV rays. This particular rubber material is more commonly used for parts that are shielded from the sun, such as automotive parts found under the hood.
Oil resistance
Oil exposure is a major challenge for many materials, which makes nitrile an appealing option. Nitrile is one of the best materials available for any parts that are regularly exposed to oil and petroleum products and can even withstand environments where these substances are extremely concentrated. TPE, like many other materials, is much more prone to breaking down when exposed to oil and petroleum.
Consumer goods
TPE is an excellent choice for consumer goods for several reasons. Parts made with TPE are soft to the touch, which is an attractive option for many parts that people will handle, such as grips on products. TPE is also slip resistant and has low toxic properties, the latter of which is a great fit for applications that require compliance with food or medical regulations.
Compression set
If your parts need to retain their original shape after being compressed, nitrile is typically a better option than TPE. Nitrile is better at rebounding back to its original shape than many other compounds, which can be very important for different seals and other parts.
Uncover Whether TPE, Nitrile, or Another Material is Right for Your Business
While there are some key characteristics that can make TPE and nitrile attractive options for your parts, finding the best choice isn’t always clear. The right material often needs to address several pain points ranging from performance requirements to budget. Fortunately, a little expertise goes a long way toward deciding which material is right for your applications.
Timco works closely with businesses to provide custom part solutions tailored to their specific needs. We partner with you to align our capabilities to your unique needs and offer you the highest value custom component solution for your business. Give us a call at 800-969-6242 or contact us online to have Timco supply your business with the parts you need for your applications.