One of Timco Rubber's main goals and objectives is to provide quality products, dedicated service and value to its customers. After 52 years of being in business, Timco Rubber is still committed to improving its processes and rubber products. In order to maintain its ISO 9001:2000 certification, Timco Rubber is audited twice a year to make certain that it is meeting expectations and delivering high quality products. [more]
One important measurement used by quality departments to measure performance is PPM (Parts Per Million). PPM represents the number of defective parts that are produced per million parts. Timco Rubber thrives for a low PPM to provide better quality products to customers as well as reduce the number of faulty parts that need to be sent back for repair or replacement. In the long run, this saves Timco Rubber money as well as ensures that customers are satisfied and their operations are not delayed due to defective parts.
For the months of January through June 2008, the average PPM per month for Timco Rubber was 789. 789 PPM results in a defect rate of .0789%. This represents a 85% decrease from the last six months of 2007 when PPM average 5,102 a month (.5102% defect rate). The management team at Timco Rubber is pleased with this significant reduction in PPM and will strive to further decrease its defect rate in the future.
Timco Rubber's Quality Policy
Timco Rubber Products pledges to deliver on time, high quality, competitively-priced products and services which conform to documented standards that will meet or exceed the requirements of our customers.
Timco Rubber Products is an ISO 9001:2000 registered company.
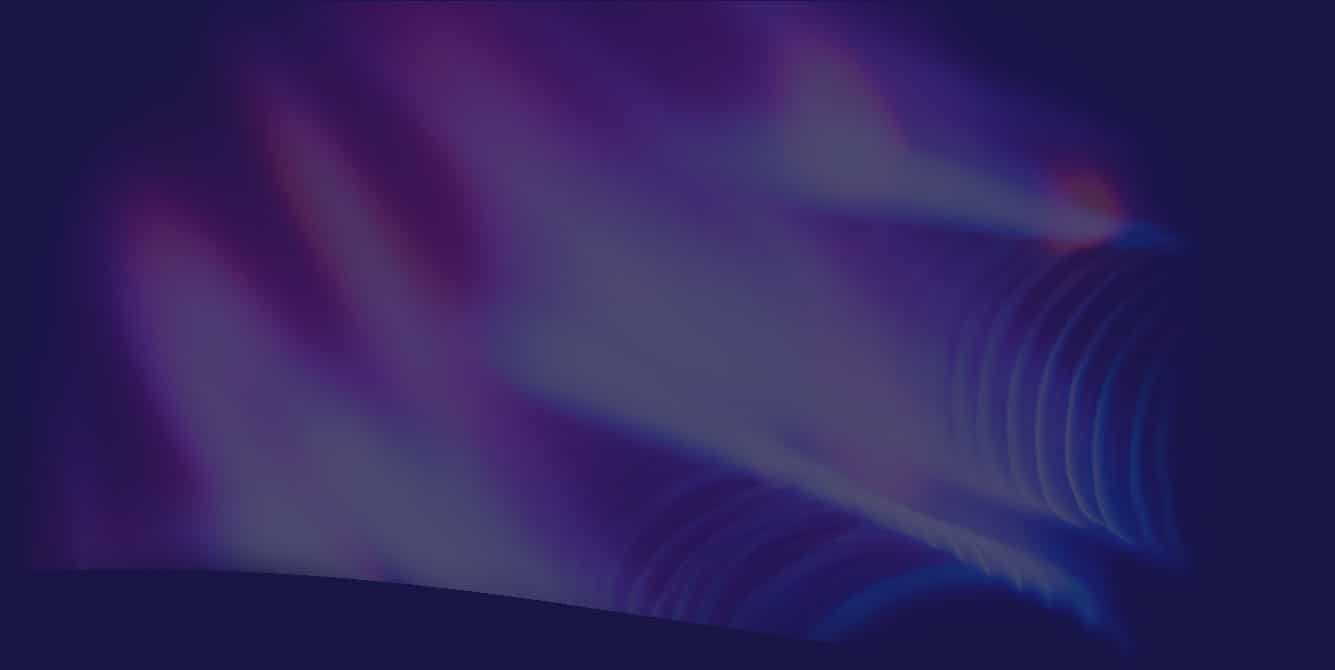