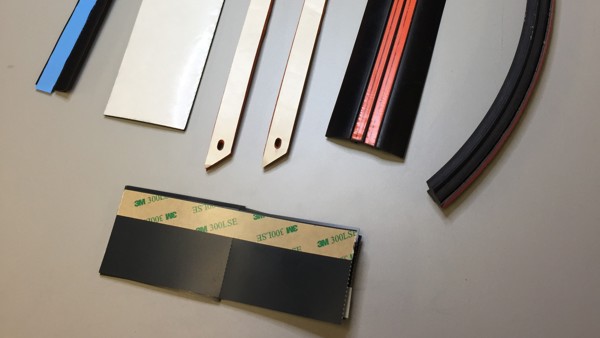
Nobody wants to get stuck trying to figure out which Pressure Sensitive Adhesive (PSA) is the right one for their custom rubber parts. Every type of material and application can call for a different solution, but the end goal is the same: have your part stick in the right spot for the required amount of time. In general, there are three types of PSAs:
- Tape with a mylar carrier
- Direct coat adhesive
- Heat-activated tape
Each of these options has its own advantages and can be a great solution depending on what you’re trying to accomplish. Here’s a quick breakdown into the different types of pressure-sensitive adhesives for custom rubber parts.
Tape with a Mylar Carrier
This tape features a plastic mylar carrier that’s roughly a thousandth of an inch thick. This carrier is coated on both sides, with one side adhering to a custom rubber part and the other to a release liner that protects the adhesive until use. Once the liner is removed, you can use the exposed adhesive to stick the part to the mating surface.
The point of the mylar itself is to provide stability to prevent stretching or shrinking of the gasket. In addition, the ability to use multiple adhesives allowing you to match your adhesion needs for both the specific material of your custom rubber part and the intended mating surface. The adhesion strength between the liner and the adhesive on the user side should be light enough to remove the liner for easy install. The bond between the adhesive and rubber gasket is meant to last.
Rubber materials bond better with specific types of adhesives. For example, you may use an acrylic adhesive with sponge rubber because acrylic will stick well and resist the oils that naturally leech out of the rubber.
Direct Coat Adhesive
Unlike the first PSA option in this post, direct coat does not include a carrier. Direct coat features a thicker layer of adhesive that’s applied to the release liner, which provides a better option for foam and sponge materials.
Thanks to its heavier coat, the adhesive can flow farther into a product to create a stronger bond with a surface. Once applied, the liner can be peeled off just like other PSAs. Another advantage to direct coats is that they are more effective on surfaces with irregularities or corners. For example, direct coats are much better for irregular surfaces than other PSA options due to the adhesive thickness.
While different, adhesive with mylar carriers and direct coats are more often used as assembly adhesives to hold rubber and plastic components in place during installation. For example, a sponge rubber sound and vibration dampener will need to stick on a surface long enough before additional parts are riveted together and trap the piece in a specific part of your application.
Heat-Activated Tape (HATs Tape)
While mylar carriers and direct coats are great for certain needs, heat-activated tape, also called HATs or HATs tape, is a much more permanent PSA solution. Heat tape/body-side molding tape features a foam that has adhesive coated on both sides. These tapes are flash heated to molecularly bond it to your rubber or plastic components, which creates a permanent bond in application.
Heat-activated tape allows you to account for irregularities of the mating surface. The foam design provides the tape with some torque resistance which allows it to accept different pressures on the adhesive. For example, a door that would close on your rubber components could cause a regular PSA option to delaminate. The foam will help absorb the difference in pressures applied across the component to keep the adhesive attached to your rubber or plastic component.
While heat-activated tape offers some notable advantages in terms of adhesion strength, those benefits are more expensive than both tapes with mylar carriers and direct coats. This means that you’ll want to weigh the needs of your applications with your budget to determine which PSA option makes the most sense for your company.
Work with Experts to Explore your Pressure-Sensitive Adhesive Options
Even with a breakdown of your adhesive options, it can be tricky to figure out which one is right for your needs. There are so many factors that come into play, such as what your application is, environmental factors, the need for permanence, your budget, and more. Fortunately, you can always turn to a trusted supplier of custom rubber parts to lead you in the right direction.
At Timco, we work with you to identify the needs of your custom rubber components. We’ll ask you a series of questions to identify any factors that may affect your application’s performance. Once we’re done, we’ll help identify some options that are best for your budget.
Ready to find a solution that sticks? Contact us today if you have any questions about custom rubber parts or request a quote to submit information on the parts you need for your project.