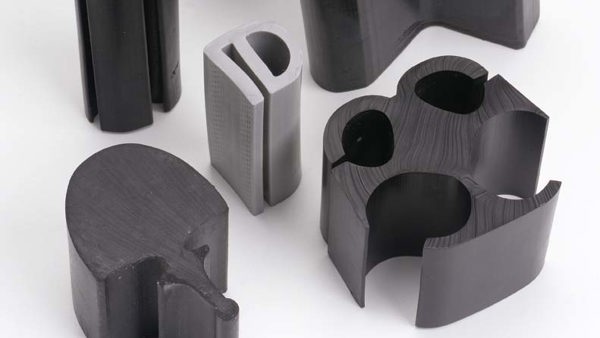
When you need seals, o-rings, or other rubber parts, it’s important that these parts are made with the right material. There are a wide range of rubber materials available, so it’s not always easy to identify which one is best-suited for your specific performance needs and budget, especially when some materials can be very similar in many ways.
Neoprene rubber and Nitrile rubber are two such materials that share several characteristics. Both materials are excellent solutions for parts that require oil resistance, but there are some key differences that can make one more viable than the other for your custom rubber parts. Let’s break down the differences between Neoprene and Nitrile to see which material is better suited for your applications.
The Differences Between Neoprene and Nitrile
While Neoprene and Nitrile are both used in environments that require oil resistance, there are a variety of reasons that can make one a better choice for your business. These are a few different factors that will impact whether Neoprene or Nitrile is right for your applications.
- Required resistance
- Part density
- Manufacturing methods and blends
- Cost
Resistances
Both Neoprene and Nitrile are natural fits for oil resistance, but not all environments pose the same problems. The amount of oil exposure has a direct impact on which material is better for your rubber parts.
Neoprene makes sense for any parts that encounter intermittent exposure to oil. Meanwhile, Nitrile is designed to handle constant exposure and environments where the oil is extremely concentrated. For example, a bowling alley uses rubber pin spotters, pulleys, and other parts that will encounter lane oil. Neoprene wouldn’t be able to hold up to the constant oil exposure, which is why the bowling industry turns to Nitrile for these applications.
Of course, there are other markets that require parts made with both materials. The automotive industry is one such example. Nitrile is typically used for a lot of under the hood applications because of the potential for regular oil exposure. Meanwhile, that same vehicle may have Neoprene hose covers, door seals, and other parts in spots where oil may occasionally reach.
Density
Part density is another potential factor that can impact your choice between Neoprene and Nitrile. Material density has a direct impact on a part’s ability to isolate vibration. The problem with Nitrile is that it’s too dense for vibration isolation.
Fortunately, Neoprene isn’t nearly as dense as Nitrile. Neoprene is used primarily used for vibration isolation applications that deal with intermittent oil exposure, such as shock absorber seals and vibration mounts. However, Neoprene typically isn’t the best option if oil isn’t an issue. If there’s no oil exposure, it’s best to use a more cost-effective material like EPDM instead.
Manufacturing methods and blends
The way your parts are made can have an impact on whether Neoprene or Nitrile is more realistic for your application. Neoprene is more commonly extruded than Nitrile, while Nitrile is often molded because of its natural connection to the automotive industry. However, both Neoprene and Nitrile can be extruded and molded to fit your needs.
One major difference between they two is that Neoprene can also be used as a sponge material, whereas Nitrile cannot. There are low, medium, and high density sponges that are purely Neoprene, which can be an attractive option for sound and vibration dampeners and other parts.
There are some sponge-like options for Nitrile, but it would need to be blended with another material. For example, PVC-Nitrile comes in a foam form that’s mostly used for die cut gaskets. However, a pure Nitrile sponge or foam doesn’t exist.
Cost
Some materials are more expensive than the other. Due to it’s added oil resistance, Nitrile is inherently a pricier material than Neoprene. As such, it will impact your budget more than other materials.
Of course, that extra cost is well worth the investment if your parts need the added oil resistance. Too much oil will lead Neoprene parts to fail prematurely, which can make Nitrile more cost-effective in the long run. That’s why it’s essential to estimate the potential for oil exposure and determine a material solution that balances both performance needs and part costs.
Find the Best, Most Cost-Effective Rubber Parts for Your Business
Neoprene and Nitrile are both viable material solutions for parts that require oil resistance. However, one likely makes more sense than the other you’re your business. That’s why Timco Rubber is here to help.
As a premium rubber parts supplier, we provide businesses with the best, most cost-effective parts for your exact needs. Out experts can work with you to uncover whether Neoprene, Nitrile, or some other material offers the most value and help you invest in the perfect parts for your budget.
Ready to solve your rubber part needs? Give us a call at 800-969-6242 or contact us online to get a quote for your project today.