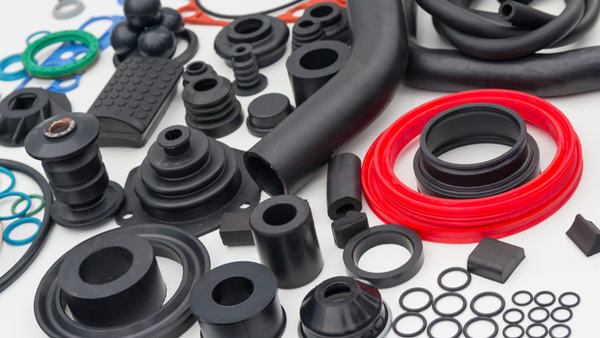
Natural and synthetic rubber are both excellent materials for a wide variety of industrial and household applications. However, the two aren’t always interchangeable.
Both polymers offer their own special physical and chemical properties that make one better suited for your parts than the other. Let’s break down a few examples of natural rubber and synthetic rubber and the key differences between the two materials.
The Differences Between Natural and Synthetic Rubber
As you may expect, natural rubber is obtained from an organic substance created with raw materials. Natural rubber is sourced from plants, the most notable of which is the Pará rubber tree, also known by the scientific name Hevea brasiliensis. Latex is procured from these plants and used to make natural rubber, which is inherently elastic a durable.
Synthetic rubber is purely a man-made material acquired through solution polymerization or emulsion polymerization. Since synthetic rubber is man-made, it can be developed into a variety of different substances with varying properties and capabilities. Some common examples of synthetic rubbers include:
Since synthetic rubber is produced artificially and open to different characteristics, these man-made polymers may cater more to specific resistances or design needs. However, the exact performance qualities of synthetic rubbers can vary greatly, which can pose challenges for anyone unfamiliar with different rubber materials or trying to identify the most cost-effective fit for their parts.
Pros and Cons of Natural Rubber vs. Synthetic Rubber
Given the range of options between natural and synthetic rubber, there are multiple factors that may dictate which option is best for your applications. These include the following criteria.
Physical durability
Natural rubber is no slouch when it comes to taking a beating. Natural rubber is an incredibly tough material that’s a great fit for any physically demanding applications such as loading dock bumpers and shock mounts. Natural rubber inherently features excellent resistance to abrasion and tearing. As such, many heavy-duty applications can benefit from natural rubber.
Of course, there are some synthetic rubber materials that also boast physical durability. There are some synthetic polymers that may be better suited for your applications if they require a little more than physical durability. For example, EPDM is a high-density synthetic rubber that combines good abrasion resistance with excellent weathering capabilities, the latter of which can pose problems for natural rubber.
Vibration and sound dampening
If you need a part to absorb vibration or deaden noise, natural rubber is a excellent option. Natural rubber typically has the compression set and high tensile strength required for shock mounts and other dampening applications.
Like before, there are also synthetic options that apply in these situations. EPDM and butyl rubber have ample deadening capabilities. Butyl in particular is great for applications that need harder materials that will essentially absorb all sound or vibration.
Resistances
If a part needs a particular resistant, you’ll typically need to opt for some form of synthetic rubber. Aside from abrasion, tearing, and electrical resistance, natural rubber won’t necessarily perform well if you have any environments that need to deal with certain temperatures, substances, or other factors.
Fortunately, there are a variety of synthetic rubber materials that are made to withstand special environments. For example, nitrile and neoprene have excellent oil resistance, while silicone is great high high-temperature applications. The exact environmental issue will dictate which polymer is best, but odds are there’s a synthetic rubber out there to address your challenges.
Invest in the Right Rubber Compound for Your Application
There are plenty of natural and synthetic rubber options available, but not all of them are suited for your specific needs. You also need to weigh the costs of each part – natural rubber and EPDM may be cheaper to produce than other types of rubber, but you’ll want to invest in the right parts if a more specialized option is necessary for success.
It’s not easy to identify the right rubber compound if you’re not an expert. Fortunately, that’s why businesses partner with Timco to identify the best, most cost-effective part solution for their applications. Give us a call at 800-969-6242 or contact us online to talk to one of our experts or get a quote for your project.