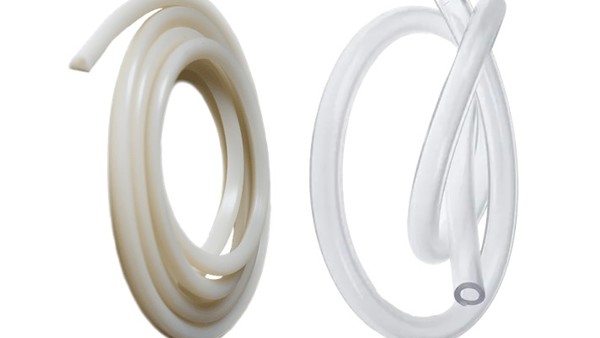
Who said that rubber and plastic have to be drastically different? TPE and PVC are two different materials that share a lot of the same benefits, even though one is rubber and the other is plastic.
From tubes to seals, TPE and PVC are both sought-after materials for durable materials that can be extruded or molded for a variety of industries. However, there are always key differences that can make one a better solution. Let’s break down each material to figure out which one is the better fit for your parts.
The Differences Between TPE and PVC
By far the biggest difference between TPE and PVC is that one is a synthetic rubber while the other is a thermoplastic. PVC was discovered by accident by German chemist Eugen Baumann but is now made by polymerizing vinyl chloride monomer and blending the resulting polymer with various formulas. TPE was invented back in 1926 and is now made by copolymerizing two or more monomers into a plastic compound.
Despite their different origins, there are some notable similarities between the two materials. both compounds can be made in soft materials that can are colorable. PVC and TPE are also excellent for outdoor applications thanks to their tremendous UV resistance and water resistance. However, there are some qualities that can make it a better fit for your needs:
- Oil and other resistances
- Hardness
- Elasticity
- Temperature range
- Recyclability
Oil and other resistances
The presence of oil can make or break the success of a lot of materials. PVC is one material that can hold its own in oily environments, making it very effective for use in the automobile industry and any other markets where oil regularly occurs.
TPE is less suited for oil exposure. This particular plastic boasts fair oil resistance, but struggles with constant oil exposure. This makes it fine for applications with occasional oil contact, but not for any design where oil regularly appears or if a large amount of it can touch the part in question.
Hardness
When it comes to hardness, PVC gives you plenty of options. PVC can be either soft or rigid, with several degrees of hardness in between. This degree of manufacturing flexibility allows engineers to utilize PVC for everything from rigid drainpipes to IV bags.
TPE also offers varying degrees of hardness, but not to the same extent as PVC. TPE is mostly known for its soft-touch features and slip resistance, making it great for consumer goods or parts that people may contact over time, such as wire or cable insulation and automotive parts.
Elasticity
Elasticity is another scenario where both materials perform admirably, however, one has a clear advantage. PVC offers good elasticity and stretchability, with a maximum elasticity of 400%, which is quite good. However, TPE is simply better at being expanded. TPE parts have a maximum elasticity of 600%, giving it a notable edge when it comes to bending or stretching preventing damage or deformation.
Temperature range
While PVC and TPE are comparable for low temperature usage, there is a notable difference for heated environments.
PVC isn’t known as a material that can withstand particularly high heat. PVC parts are typically able to withstand up to 140 degrees Fahrenheit – not a bad limit, but certainly not one for tougher environments. TPE does offer more heat resistance with a high-end usage of up to 250 degrees, giving you some more flexibility in hotter applications.
Recyclability
If sustainability or recycling initiatives are important to you, TPE is an excellent material option. Unlike most rubbers, TPE parts can be repurposed through molding and extrusion, making it one of the more eco-friendly material solutions available. TPE also consumes far less energy than similar materials, making it more sustainable in multiple ways.
PVC can be recycled, but not nearly as easily as TPE. Similar to recycling silicone, the process to reprocessing PVC is both more complicated and more difficult, which can be an immediate downside for businesses trying to meet sustainability goals.
PVC vs. TPE: Invest in the Right Material for Your Parts
Is TPE better than PVC? It ultimately depends on what your business is trying to accomplish. There are pros and cons to each part, so you’ll need to evaluate your ideal performance requirements and weigh your options.
Fortunately, you don’t need to go through that process alone. Timco works with businesses to uncover the best, most cost-effective solution for your parts. Give us a call at 800-969-6242 or contact us online to talk to one of our experts about the parts you need.