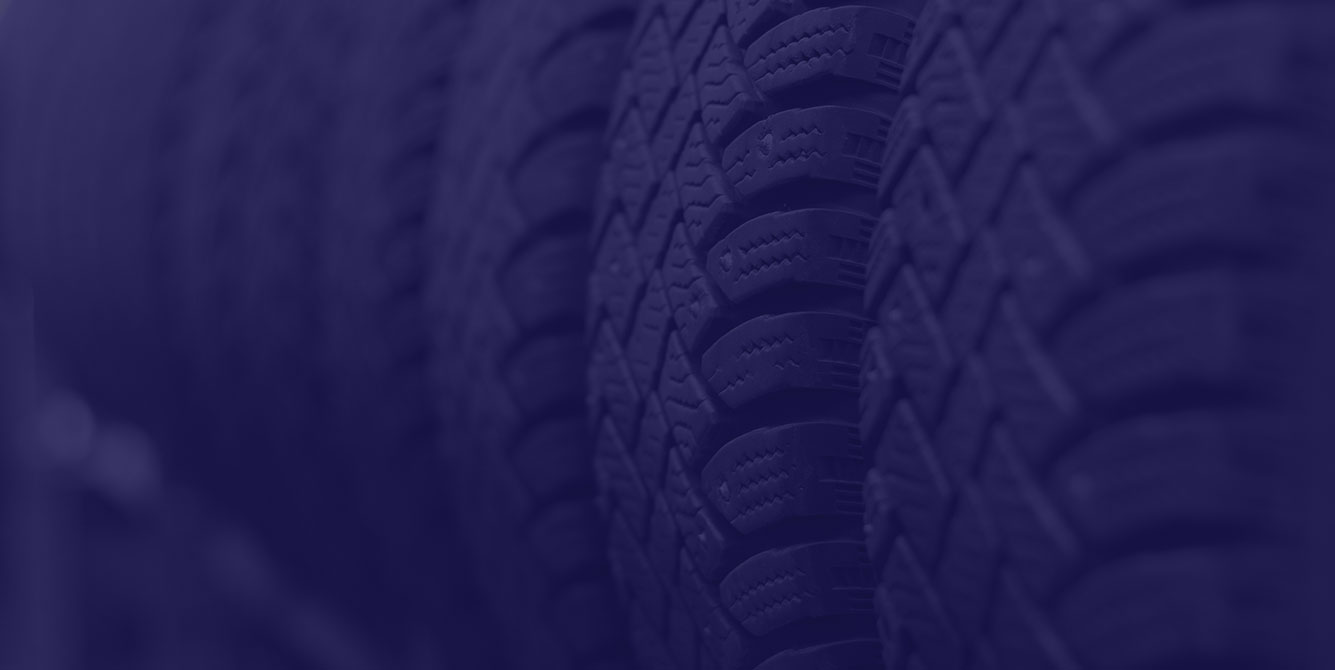
Natural Rubber Products Supplier
Gaskets, O-Rings, Seals, Shock Mounts, Bushings & More
When you need a tough material, natural rubber is an abrasion-resistant solution that’s great for areas where other materials would wear out. Timco Rubber can work with your business to provide custom-designed natural rubber parts that are specifically designed for your applications.
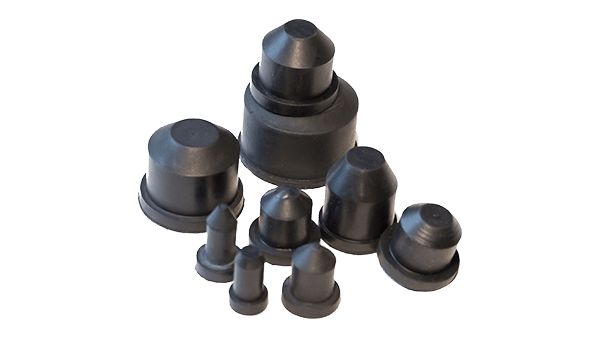
Natural Rubber: Tough Parts for Physically Demanding Applications
Some applications demand the most out of their individual parts. Natural rubber is a versatile material used in engineering for many years for a very simple reason – it can take a beating and still perform crucial functions.
Natural rubber combines high tensile and tear strength with an outstanding resistance to fatigue. These heavy-duty capabilities make this material an ideal polymer for dynamic or static engineering applications that deal with regular vibration, noise, contact, and other issues. These qualities make natural rubber an ideal solution for tires, printer rollers, agitators, and other parts that will come into regular contact with abrasive surfaces or other damaging elements.
What is Natural Rubber?
While most types of rubber are made in labs and polymerized to develop compounds with specific properties, natural rubber has been harvested from dandelions and other plants since 1,600 B.C. Modern day natural rubber can be traced back to 1736, with the Amazonian rubber tree (Hevea brasiliensis) in South America being serving as the most common source for rubber latex.
The general way to make rubber involves taking latex from rubber tree plantations or other sources and adding a few other ingredients. In general, these ingredients include acids, chemicals, and additives to create the material classically associated with car tires, rubber bands, and other parts, as well as a variety of products ranging from shock mounts to pad assemblies
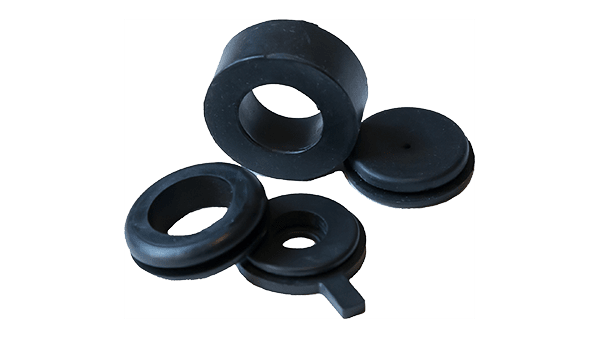
Natural Rubber Properties
- Common Name: Natural Rubber
- ASTM D-2000 Classification: AA
- Chemical Definition: Polyisoprene
- Temperature Range
- Low Temperature Usage: -20° to -60° F | -29° to -51°C
- High Temperature Usage: Up to 175° F | Up to 80°C
- Tensile Strength
- Tensile Range (P.S.I): 500-3500
- Elongation (Max %): 700
- Durometer (Hardness) – Range: 40-90 Shore A
- Resistance
- Abrasion Resistance: Excellent
- Tear Resistance: Excellent
- Solvent Resistance: Poor
- Oil Resistance: Poor
- Aging Weather/Sunlight: Poor
- General Characteristics
- Adhesion to Metals: Excellent
- Compression Set: Excellent
- Resilience - Rebound: Excellent
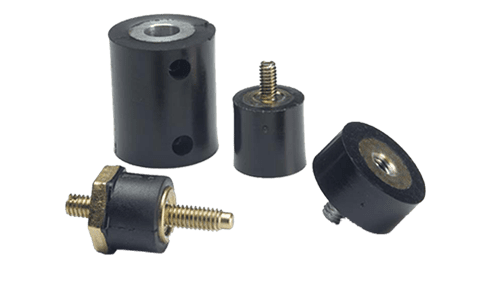
Natural Rubber Applications
- Mining
- Truck liners
- Crusher cones
- Lining and skirting
- Rubber sleeves
- Belt scrapers
- Feed plates
- Material Handling
- Conveyer systems
- Bumpers and guards
- Liners
- Loading dock bumpers
- Heavy Equipment
- Body pad assemblies
- Oil and Gas
- Vibration isolators
- Water and Air Filtrations
- Rubber elbows
- O-rings
- Hose and tubing
- Industrial Machinery
- Machinery mounts
- Vibration isolators
- Machine pads
- Agriculture
- Isolation mounts
- Bushings
- Tires
- Medical
- Braces and supports
- Protective covers
- Rubber caps
- Instrument handles
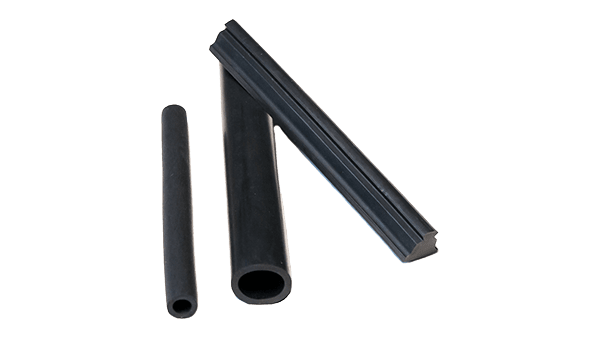
Natural Rubber Benefits & Advantages
- Can be compounded to meet nearly any mechanical requirement
- Ability to be electrically insulating or fully conductive
- Features natural protection, insulation, and sealing properties
- Excellent ability to absorb vibration and shock while silencing noise in even heavy-duty applications
Timco: Complete Custom Natural Rubber Part Solutions
The level of durability, physical characteristics, and ease of manufacturing makes natural rubber an excellent option – but only if it’s right for your parts. Timco collaborates closely with businesses to provide tailored part solutions that align with their specific performance specifications and budgetary constraints.
In addition to personalized service, we also strive to make the part supply process simpler and more convenient. We provide several value-added services designed to streamline your processes:
- Subassembly of TPE parts
- Kanban replenishment
- Kit assembly
- Flexible control methods
- Efficient logistics and just-in-time delivery
Natural Rubber FAQs
<h3> Q: What is Natural Rubber and what are its primary applications? </h3>
Natural rubber is a polymer derived from the latex sap of the rubber tree (Hevea brasiliensis). Unlike synthetic rubbers, this sap is a renewable and biodegradable material known for its exceptional elasticity, resilience, and tensile strength. Primary applications include:
- Industrial Goods: Belts, agitators, hoses, and rollers
- Automotive Industry: Tires, seals, dock bumpers, pad assemblies, bushings, and gaskets
- Agricultural Products: Tires, shock mounts, pad assemblies, isolation mounts
- Adhesives and Sealants: Various bonding applications
Q: What are the key properties of natural rubber?
Natural Rubber possesses a few different characteristics that make it attractive for various industries, most notably being its physical durability. Natural rubber is excellent at both absorbing vibration and shock while withstanding regular contact with abrasive surfaces and other forms of wear. Natural rubber also offers:
- Either electrical insulation or full conductivity based on formulation.
- Excellent compoundability for nearly all mechanical needs.
- High tensile strength and stretchability.
- Impressive compression set and resilience.
Q: How does natural rubber compare to synthetic rubbers like EPDM, neoprene, or Viton?
Natural rubber is often chosen for its outstanding toughness and cost-effectiveness, while other materials offer special resistances that natural rubber may lack. EPDM provides added weathering resistance, while both silicone and Viton are excellent high-temperature rubbers that can thrive in hot environments with oils and other substances that would damage natural rubber.
Q: What are the advantages and disadvantages of using natural rubber?
- Advantages:
- Physical durability: Thrives in applications wear that require an ability to hold up to shock, abrasion, and other forms of physical wear.
- Environmental sustainability: Derived through naturally available resources and is biodegradable.
- Durable under stress: Boasts excellent resilience and compression set.
- Disadvantages:
- Limited chemical resistance: Breaks down when exposed to oils, fuel, and many chemicals.
- Temperature range: Doesn’t offer the high-end heat resistance of some specialty materials.
- Weathering: Prone to degradation when exposed to sunlight, water, and other outdoor elements.
Q: Is natural rubber suitable for medical and healthcare applications?
Yes, natural rubber is a viable option for certain medical and healthcare applications. Natural rubber’s flexibility, durability, and biocompatibility make it a fit for some tubing, supports, and other parts needed by this industry.
Q: What is the typical lifespan of natural rubber products?
The lifespan of natural rubber depends on the usage, maintenance, and environmental conditions posed on those parts. Natural rubber can generally last up to 5 to 10 years with proper care and ideal working conditions.
Q: How should natural rubber be maintained to ensure longevity?
Maintenance Tips:
- Regular inspection and care: Check for signs of cracks, deformation, and other issues. Clean parts with mild detergents if possible for the application.
- Proper storage: Store off the ground in a cool, dry place that isn’t exposed to direct sunlight or substances that will degrade the material.
Q: Can natural rubber be recycled, and if so, how?
Yes, natural rubber can be recycled. As it is made from a naturally occurring substance, natural rubber will degrade over a long period of time. Certain recycling facilities can use different methods to repurpose natural rubber, such as grinding it and incorporating natural rubber in new products, or devulcanizing the material to allow for reprocessing.
Interested in natural rubber vibration isolators, bushings, and other parts?
Call 1-888-754-5136 to find out more, or get a quote for rubber dock bumpers, shock absorbers, and other natural rubber products.
Not sure which material you need for your custom rubber product? View our rubber material selection guide to learn more about which compound is perfect for your performance needs.
Want to make sure that Timco is the right partner for all your Natural Rubber part requirements?