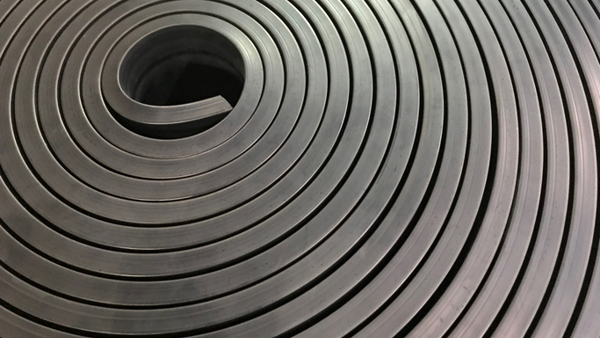
A material can have all the qualities you want, but it won’t matter too much if it doesn’t last.
EPDM is a high-density synthetic rubber known for its versatility and cost-effectiveness. It’s combination of durability and resistances to aging, abrasion, and heat have made it a popular option for everything from industrial applications to roofing. Let’s break down just how long EPDM can last and the different factors that can shorten that lifespan.
The Expected Lifespan for EPDM Parts
In general, rubber materials can last years to decades depending on the compound and how you plan to use it. EPDM specifically has an estimated shelf life of up to 15 years depending on the application and can remain functional for decades. For example, one study found that EPDM roofing had a minimum age of 30 years and a possible service life of more than 50 years.
Of course, a part’s lifespan is also dependent on its working conditions. A more passive part like an EPDM roofing membrane won’t have to deal with as much wear and tear. However, an EPDM compressor grommet for an outdoor HVAC unit will likely degrade at a quicker pace. Even in storage, too much exposure to the elements will age rubber to various degrees.
What Can Shorten EPDM’s Lifespan?
The good news is that EPDM is a durable, long-lasting rubber material for a variety of parts. Still, it’s important to take care and use EPDM in the right situations.
EPDM can last for decades, but there are different environmental hazards that can and will drastically shorten its lifespan. Those hazards include:
- Oil: Exposure to oil is one of the biggest threats to EPDM parts. Unlike materials like neoprene and nitrile, oil will cause EPDM to degrade or even swell with too much exposure.
- Solvents: A variety of solvents can cause EPDM parts to prematurely break down. Examples of problem solvents include everything from water to chemicals like acetone and methanol.
- Extreme temperatures: EPDM can withstand temperatures ranging from -60 to 350 degrees Fahrenheit, but it does have a limit. Parts made with EPDM can shrink, stretch, and crack when exposed to temperatures outside its limit for long periods.
- Flame: While EPDM is stable in high temperatures within its range, it is not flame resistant. EPDM can catch fire, although additives and blockers can be added to improve flame resistance.
- Tearing: EPDM offers great physical durability to most wear and tear, but tearing can pose some problems. If tearing is a major threat, you may need to consider a material like butyl or Viton.
Invest in Long-lasting EPDM Parts
EPDM is an excellent material for many industries, but it’s not always easy to find the right compound for your exact needs. Whether you need a specific formulation of EPDM or a different rubber material altogether, Timco can help.
We work closely with business to supply them with custom rubber and plastic parts designed around their performance criteria and budget. Give us a call at 800-969-6242 or contact us online to talk to one of our experts about your part needs.