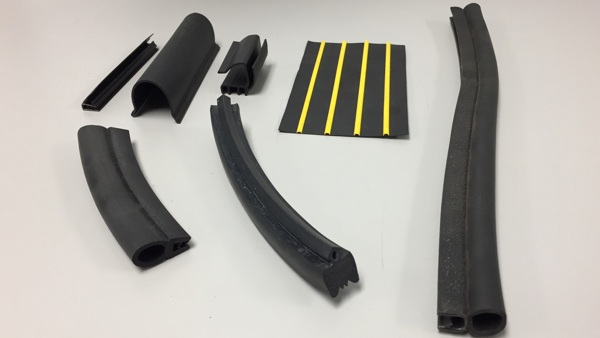
The right co-extruded rubber or plastic parts can really help your applications come together. While typical extrusions are made with only a single material, co-extruded components can combine two different rubber or plastic materials into a single extruded part, allowing you to take advantages of each material’s natural characteristics.
Typically, co-extruded rubber or plastic parts, also known as dual durometer extrusions, allow you to have both rigid and soft materials in the same component. The rigid material allows the components to create a strong connection to metal, while the softer material is generally used as a flexible seal. This combination gives you the best of both worlds: the strength of a clip section with the flexibility of a seal section.
How are Co-Extruded Parts Made?
During co-extrusion, both materials are extruded at the same time. Each material has its own initial die before the two separately extruded pieces are fed into a mating die that locks the two together. After that, the combined extrusion goes through a curing system which seals both materials together permanently.
Co-extruded parts can be made with compatible rubbers or plastics. Various types of rubber and sponge rubber or rigid and flexible plastic materials can be combined into a single, extruded part. Of course, the materials selected must be chosen to best serve the needs of your application and your budget.
Factors That Can Impact Your Custom Co-Extrusions
The rubber and plastic materials used for co-extruded components can vary greatly. Not only do you need to weigh whether plastic or rubber is a better choice, you have to determine which types of plastic or rubber are right for your components. The needs for each piece are application and customer-specific, so there is no one-material-fits-all solution. Instead, it’s important to weigh several factors that can narrow down which materials are best suited for your needs.
Temperatures and environments
Some materials are better at handling extreme temperatures or specific environmental conditions than others. For example, both rubber and plastic will harden in the cold, but certain plastic may be better for use in sub-zero temperatures, such as what a door seal for a freezer might experience. The presence of water, sunlight, chemicals, and other factors can each play a part in determining which materials make the most sense.
Adhesives
The need for adhesives can play a part in the decision process. While you can put adhesives on plastics, it’s generally easier to do so on rubber. This can mean that adhesives made for plastics can be more expensive, so rubber may be a more cost-effective solution unless you need some form of plastic that is better for the overall requirements of the component and application.
Recyclability
If your business places an emphasis on being environmentally friendly, certain plastics may be a better option than some rubber materials. Plastics like PVC are recyclable, which means it can be reground and used for future extrusions. This beneficial when green technology and practices are a major selling point for you or your end consumers.
Use of colors
Co-extrusions don’t always need to be in various shades of black. While rubber doesn’t give you many options, you can have colorant added to plastics to give you access to many different colors for your products. For example, a bright yellow for safety applications or part that require high visibility.
Tooling costs
The initial tooling cost for rubber co-extrusions are typically lower than plastic co-extrusions. This can mean that you’ll need to weigh the benefits of certain materials versus their upfront costs, which includes the price involved with making a custom die and both time and labor requirements connected with your components.
Custom Co-Extruded Components Made with Your Needs in Mind
It’s not always easy to figure out which materials make the most sense for your applications. Many rubber and plastic materials cross over in terms of their features, so there’s not always a distinct line where one option is better than another. When this happens, you’ll want to work with a supplier of custom rubber and plastic parts that not only knows how to cater to your needs, but can also provide high-quality co-extruded rubber and plastic products.
When you work with Timco, we can help you weigh all the factors that go into material selection. Once we understand your application and your budget, we can give you our expert take on what is the best for your application and provide additional options. Contact us today if you have any questions about custom extrusions or request a quote to submit information on the components you need for your project.