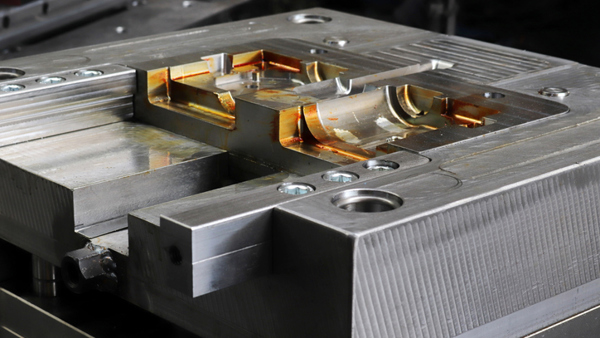
Ethylene Propylene Diene Monomer, also known as EPDM, is an incredibly versatile material, both in terms of performance capabilities and manufacturing. This particular material can be fabricated in many ways. But is it possible to injection mold EPDM rubber?
The short answer is yes. It is not only possible to injection mold EPDM, the compound works well with compression and transfer molding processes as well. Let’s examine the benefits of injection molded EPDM and how the process works.
Why Injection Mold EPDM?
While injection molding was originally used for plastics, the process has been used for various natural rubber and synthetic rubber compounds for more than half a century. Injection molding can utilize a wide range of materials, which includes EPDM.
There are several advantages to injection molding rubber compounds like EPDM. These benefits include:
- The ability to efficiently achieve high volume production.
- The potential for a lower price per unit as more parts are produced.
- Excellent precision that yields tremendous part consistency and reliability through a repeatable process.
- Quick cycles times that can produce many parts in a short period of time.
- Much lower scrap rates and overall excess material waste as compared to other more traditional manufacturing means.
There are also multiple reasons why businesses would want to use EDPM specifically for rubber injection molding. EPDM is resistant to UV exposure, ozone, aging, weathering, steam, water, and many chemicals. EPDM is also stable in high and low temperatures. These capabilities give EPDM a long-term life span and make it a tremendous option HVAC, automotive, and other industries.
A Quick Breakdown of the EPDM Injection Molding Process
A basic explanation of injection molding is that it takes a specific material, heats it, and injects it into a closed metal mold. The cavity of the mold is what gives each piece its shape and design. Molds can be custom built to accommodate special designs or maximize the parts made per cycle.
The process starts by closing the mold and injecting the heated EPDM into the exposed mold cavity. A predetermined amount of EPDM is broken down into smaller strips and fed into a screw to break them down for injection.
As the mold fills, displaced air escapes through vents to prevent air bubbles and any other imperfections. A key difference between injection molding plastic and rubber compounds like EPDM is that rubber is heated and placed under significantly more pressure per square inch of cavity surface. While plastic is cooled under less pressure, high pressure and elevated temperature helps plasticize the parts to cure the compound and plasticize the individual pieces.
Each cycle of parts is given a varying amount of time to fully cure – the exact length depends on the specific design. Once finished, the mold opens and the parts are ejected or manually removed so that the process can begin again. For a more in-depth explanation of injection molding, check out our rubber molding process guide.
What EPDM Parts Can Be Injection Molded?
As a versatile material, EPDM is commonly injection molded into a wide range of rubber products and parts. These parts can include, but are not limited to:
- Grommets
- Gaskets
- Drain tubes
- Formed hoses
- Spacers
- Dampers
- Vibration isolators
- O-rings
- Covers
- Diaphragms
- Bellows
Work with a Trusted Custom Rubber Parts Supplier for Your Molding Needs
When you need quality parts, it’s important to work with a quality partner. Timco Rubber has more than half a century worth of experience supplying businesses with injection, transfer, and compression molded parts for their applications.
At Timco, our goal is to deliver customized solutions that allow you to maximize engineering methods to address your specific performance requirements. This process allows our experts to help you invest in the best, most cost-effective molded rubber products for your applications.
Are you in need of quality rubber and plastic parts? Give us a call at 800-969-6242 or contact us online to talk to one of our experts or get a quote for your project.